- Как сделать нож своими руками
- Как сделать нож своими руками в домашних условиях: пошагово
- Набор ножей для резьбы по дереву своими руками
- Как сделать резцы по дереву своими руками
- Инструмент для резьбы по дереву своими руками: стамеска, резцы и ножи
- Какие Заточные станки для ножей: виды, советы по выбору, изготовление своими руками- Обзор +Видео
- Ковка ножа своими руками | Строительный портал
- Изготовление ножей с помощью основных инструментов: 13 шагов (с изображениями)
- Инструменты, необходимые для создания цеха по изготовлению ножей
- Начало изготовления ножей – какое оборудование мне нужно?
- Информационный центр изготовителя ножей своими руками: набор инструментов для начинающих
- Как сделать нож
- Хобби изготовления ножей
- Полное онлайн-руководство по изготовлению ножей, ИНСТРУМЕНТЫ ТОРГОВЛИ – Изготовление ножей Berg
Как сделать нож своими руками
Многие часто задаются вопросом – насколько сложно самостоятельно изготовить нож? Потому что мужчина, как известно должен не только вырастить дерево, построить дом и родить сына, но и обязательно должен сделать своими руками настоящий нож. В этой статье мы вкратце расскажем, об основных способах самостоятельного изготовления ножей со всадным типом монтажа. Для этой цели вам понадобится клинок (или металлическая заготовка), материал для рукояти, металл для изготовления оковки.
Что необходимо для изготовления рабочего образца
Вам понадобятся следующий минимальный набор инструментов:
-
Электрический лобзик (или «болгарка»). При желании можно обойтись ручной ножовкой по металлу. Эти инструменты нужны для выпиливания клинка из металлической заготовки.
-
Набор напильников, наждачная бумага, шлифовальные камни. Эти инструменты нужны для точной подгонки заготовки в размер, а также для выведения спусков. Если у вас имеется электрический точильный станок, то все эти процедуры вы проделаете быстрее и легче.
-
Электрическая дрель и набор сверл. Дрель вам понадобится для сверления отверстий в заготовке клинка и заготовке для рукояти.
-
Струбцина для плотного соединения клинка и рукояти.
Из материалов вам потребуется:
-
Эпоксидный клей;
-
Натуральное льняное масло или воск;
-
Финишный лак;
-
Малярный скотч.
Если вы первый раз делаете нож самостоятельно, то мы рекомендуем приобрести в ножевом интернет-магазине готовый клинок, заготовку для рукояти из стабилизированной древесины и готовую оковку. В этом случае вам потребуется лишь подогнать рукоять до нужных размеров, вставить клинок в рукояти и склеить.
Для новичков, которые планируют пройти весь процесс изготовления самостоятельно важно знать, что наиболее простым в изготовлении является нож северного типа с прямым обухом и спусками на одну треть.
При самостоятельно изготовлении ножа желательно ознакомится с ГОСТами, в которых содержится описание признаков холодного оружия. Важно понимать, что самостоятельно изготовить можно только туристический нож, который не соответствует признакам холодного оружия.
Процесс самостоятельного изготовления ножа состоит из следующих этапов. Нарисуйте на плотной бумаге клинок с хвостовиком. Вырежьте клинок из бумаги и перенесите контур на металлическую заготовку. Таким же образом нанесите контур оковки.
С помощью электрического лобзика вырежьте клинок и оковку из заготовки. Вырезая клинок, делайте небольшие допуски 3-5 миллиметров в большую сторону. Потом обработайте клинок напильником до полного соответствия размерам.
На обеих сторонах клинка нарисуйте несмываемым маркером линию спусков. Закрепите клинок в тисках (или с помощью струбцины на столе) горизонтально и параллельно полу. Грубым напильником сточите клинок в направлении от линии спуска к режущей кромке. Эта операция называется «выведение спусков». Если у вас есть электрический точильный станок, то вывести спуски можно с его помощью.
Нанесите на оковку контур отверстия под клинок. Рассверлите и пропилите отверстие до нужных размеров.
В заготовке для рукояти с торца просверлите отверстие для хвостовика. Глубина отверстия должна быть чуть длиннее хвостовика. Соедините клинок и оковку. Залейте отверстие в деревянной заготовке эпоксидным клеем. Вставьте хвостовик в отверстие, деревянной струбциной сожмите клинок и рукоять. Оставьте на 10-12 часов.
После того, как клей застынет, обработайте деревянную заготовку рукояти напильником до нужных размеров. Заточите клинок на нужный угол и обработайте рукоять льняным маслом или воском. После того как мало или воск впитаются и высохнут, покройте рукоять тонким слоем финишного лака. Поздравляем, ваш первый нож готов!
Как сделать нож своими руками в домашних условиях: пошагово
На чтение 10 мин. Просмотров 544 Опубликовано Обновлено
Пару сотен лет назад, нож был орудием выживания, и делали их мастера, обученные этому делу. Сегодня прогресс развитого человечества позволяет купить его в любых магазинах. Производство ножей перешло в массовое изготовление, и теперь изделие доступно каждому желающему. А как сделать нож, применяя технологии прошлого – мало кто знает.
Древний самодельный нож.Разновидности ножей и их назначение
Нет ничего идеального в этом мире. Это касается и ножей. Каждое изделие предназначено для определённых целей. Качества и характеристики его будут соответствовать поставленным задачам.
Придавая ножу твёрдости, неизбежно добавляется хрупкость.
Немало зависит от качества стали, но физику не обманешь. Специалисты выделяют четыре основных направления изделий:
- Кухонные ножи.
Наиболее популярными с лёгкостью можно назвать – кухонные ножи. К клинкам таких изделий предъявляются требования повышенной твёрдости и одновременно исключение хрупкости.
Нож, сталкивающийся с разделыванием небольших тушек птиц и животных, обязан иметь хорошую остроту и не сломаться о кость при нагрузке. Добиваются этого с применением в изготовлении специальных марок стали и её закалки.
- Любители активного отдыха выбирают – туристический вариант. Клинок предназначается для решения мелких бытовых походных задач. Иногда используется в качестве топора. Целесообразно оснастить такой клин хорошей режущей кромкой и достаточно толстым обухом.
- Одна из разновидностей туристического клинка – ножи выживальщика. Производство ножей такого типа подразумевает внесение особых конструктивных характеристик. Многое в одном. Стропорез, пила, серрейтор, отвёртка и другие качества сочетаются в этом ноже. Нагружая клинок множеством функций, теряется прочность изделия.
- Охотничьи ножи.
Наиболее требовательные и заслуживающие особого внимания – охотничьи ножи.
Высокая твёрдость клинка, долго держащая заточку режущая кромка и ударная вязкость – обязательные требования к изделию.
Нож обязан справляться со всеми задачами, перечисленными в предыдущих пунктах. При необходимости он становится кухонным прибором, походные задачи должен решать с лёгкостью, и в крайнем случае стать – ножом для выживания.
Некоторые поставленные задачи решить одним клинком невозможно. Чисто конструктивно не целесообразно. Рекомендуется использовать несколько небольших изделий, чем нагромождать один нож кучей функционала.
Преимущества самодельных ножей
Производство ножей приобрело массовость. Это часто сказывается на качестве самого изделия. Особенно благодаря китайским братьям, часто встречается ширпотреб, что и ножом назвать сложно. Люди хотят иметь качество за небольшую плату.
В магазинах за оригинальные клинки известных брендов, просят неприлично крупные суммы. Обратиться к профессиональному кузнечному мастеру – ценник выйдет ещё дороже, учитывая неповторимость и оригинальность изделия.
Брендовый японский нож от компании HATTORI.Остаётся надежда только на себя. Но как сделать нож, не имея должного опыта – вопрос нелёгкий. Статья ориентирована ответить на него. Но в начале преимущества изготовления ножей своими руками:
- нет необходимости подбирать в магазине или объяснять мастеру, что требуется – вы прекрасно представляете, чего хочет душа;
- изучив поверхностно характеристики сталей, выбрать сплав можно самому;
- полученные знания помогут правильно выковать и закалить клинок;
- рукоять и дизайн изделия – полностью в ваших руках.
Сделать нож своими руками в домашних условиях, вполне реально. При первых попытках могут произойти непредвиденные ситуации, отчаиваться не следует, терпение и труд – залог успешного результата.
Из какой стали лучше сделать нож
Стальные заготовки.Выбирая сталь для изготовления ножа, необходимо внимательно изучить её характеристики. Зная поведение металла при различных условиях, несложно подобрать вариант, интересующий вас.
Достаточно много сплавов металла имеют подходящие характеристики для изготовления клинка. Основными достоинствами называют:
- твёрдость сплава и его прочность – подвержено меньшей деформации, но хрупкость увеличивается. Эти два качества непременно пересекаются между собой;
- износостойкость – исключит частую заточку режущей кромки. Иначе клинок сотрётся до состояния шила;
- коррозийная стойкость – заключается в противостоянии влаги. Нержавеющая сталь имеет в составе большое количество хрома, что сказывается на прочности и твёрдости изделия;
- сопротивление механическим воздействиям – характеризуется выдержкой режущей кромки к затуплению.
Мастера пытаются удерживать баланс этих качеств в одном изделии. Сделать это – непросто. Но некоторым клинкам необходимо одно конкретное качество, это упрощает задачу. Марки стали нужные обычному человеку, доступны в профильных организациях.
Сломанный клинок.Сплавы, производимые в России, имеют множество зарубежных аналогов, схожих по структуре. Аббревиатуры содержат другие буквы и цифры. Несколько примеров:
- 8Cr13Mov – отлично затачивается в составе немало углерода, неплохой вариант, цена – качество. Имеет широкое распространение благодаря доступной цене;
- ATS-34 – японский вариант с хорошей коррозийной стойкостью и немалой прочностью. Хорошо держит заточку, относится к сплавам премиального класса;
- 440С – нержавейка имеющая универсальность в применении, отличается низкой стоимостью. Хром и углерод делают её износостойкой и придают хорошую сопротивляемость ржавчине.
Для изготовления ножей своими руками изучите свойства металла. Металлурги – люди нежадные, всегда поделятся полезной информацией. Обладая ею, обработка металла станет на порядок проще.
Какой инструмент понадобится
Производство ножей дело не простое. Требуется не только опыт, но и специфический инструментарий. Изготовить нож своими руками от начала до конца, затребует немало времени. А такие приспособления, как ленточная шлифовальная машина или станок, сократят его до минимума.
Шлифовальный станок.Учитывая другой электроинструмент, сама практика самодельного изготовления может выйти в копеечку. Многое зависит от способа изготовления и материала.
Если понадобится ковка изделия – это дополнительные инструменты и приспособления. Новичкам рекомендуется начинать с более простых вариантов изготовления.
Для этих целей возьмём сталь 1095 с высоким содержанием углерода, хрома и марганца. Она хороша при заточке режущей кромки, но под бритву выводить не рекомендуется – быстро затупится. Рукоять изготовим из дерева с накладным методом монтажа. Инструменты понадобятся следующие:
- бумага, карандаш;
- дрель с набором свёрл разного диаметра;
- медный или латунный пруток для клёпок;
- тиски, молоток;
- ленточный шлифстанок или УШМ с отрезным и шлифовальным кругами;
- муфельная печь или горн;
- духовой шкаф газовой плиты;
- моторное масло в ёмкости;
- напильники разного зерна;
- ножовка по дереву, лобзик;
- эпоксидный клей, струбцины;
- масло, воск или специальная пропитка для дерева;
- наждачка разной зернистости.
Отсутствие шлифстанка, допустимо заменить болгаркой. Но с ней работать сложнее. Если нет печи или горна, существует вариант использования каменного угля на открытом воздухе с подачей воздуха.
Опасный но нужный инструмент.Смысл заключается в том, что вполне допустимо заменять некоторые инструменты и приспособления, аналогичными, что имеются в наличии. Применение смекалки – не возбраняется.
Пошаговая инструкция по изготовлению ножа своими руками
Для рукояти необходимо найти брусок хорошей древесины: бук, вишня, берёза, дуб, слива и другие породы подходят неплохо. Заготовка не должна быть пересушенной. Выполняя инструкцию поэтапно, начинающий мастер справится с этой нелёгкой задачей. Процесс изготовления ножа без применения ковки, выглядит так:
- Обязательно необходимо изобразить в виде рисунка желаемый результат. Все работы следует проводить в соответствии с этим шаблоном. Если не хватает фантазии, подглядите в профильных интернет-ресурсах. Попадаются эскизы с разметкой размеров.
- Затем следует перенести рисунок на пластину металла. Для начала только общий профиль. На основании его вырезаем с помощью ленточного отрезного станка заготовку. Имея такой инструмент – вы сократите время и количество потраченных нервов. Иначе зажимаем пластину в тиски и колдуем с помощью болгарки.
- Приготовьте средства индивидуальной защиты: перчатки, респиратор и очки. Работа на шлифовальном станке – искристая и пыльная. Необходимо привести заготовку в надлежащий вид. Убрать все заусенцы и довести её до состояния эскиза. Необходимо следить за температурой металла, появление тёмных пятен, свидетельствует о перегреве. Этого желательно не допускать, в дальнейшем скажется на качестве изделия. Чаще опускайте заготовку в ёмкость с водой для остужения.
- Ответственный этап формирования скосов. Необходимо определиться с будущим использованием клинка. Для рубки и тяжёлых задач, лезвие оставить толще. Нежели необходим тонкий рез продуктов или требуется бритвенная заточка – изделие необходимо сточить равномерно с обеих сторон. Но переусердствовать не следует на этом этапе. Снять излишки допустимо после закалки.
- Медный пруток надобно разрезать на небольшие кусочки для клёпок в рукоять. И в соответствии с их диаметром насверлить отверстия в хвостовике клинка. Делается это до закалки изделия.
- Закалка.
Закалка стали необходима для придания твёрдости клинку. Изучив металлургическую справочную таблицу про углеродистый сплав 1095, становится ясно, что закалку проводить необходимо при температуре в 800 градусов.
Что позволит получить твёрдость в пределах от 59 до 63 HRC.
Нагрев клинок до необходимой температуры, охлаждение проводится в моторном масле, в течение трёх секунд. Затем оставьте остывать на воздухе.
- После процедуры закалки обязательно производится отпуск клинка, иначе он будет хрупким и при малейшем ударе есть вероятность расколоть его. Духовой шкаф газовой плиты нагреваем до 200 градусов. Затем аккуратно помещаем в него заготовку и оставляем на два часа. После изделие получит все необходимые качества добротного клинка.
- Теперь надобно довести спуски до ума. И вывести режущую кромку. Предварительно убрав с изделия весь нагар шлифовальной машиной.
- Монтаж рукояти, начинается с располовинивания бруска. Затем две части следует разметить в соответствии с эскизом и лобзиком вырезать симметричные заготовки. Насверлить в них отверстия с точностью, как на хвостовике и склепать медными шлицами. Предварительно для надёжности промазав эпоксидкой. Оставить высыхать на 24 часа, сжав изделие струбцинами. Затем на шлифмашине придать рукояти необходимый вид, и промазать дерево льняным маслом или пропиткой.
Краткая инструкция порядка действий при изготовлении ножа. Как сделать нож, теоретически понятно. Надеемся, что статья пригодится и на практике.
Правила заточки готового изделия
Правильно эксплуатируя клинок в условиях его предназначения, он неизбежно потеряет остроту. Этот процесс происходит на микроскопическом уровне при трении металла о разрезаемые предметы. Совершенно естественная потеря остроты требует больших усилий для реза. Постепенно становится ясно, что нож требует заточки.
Острый нож.Если нож изготовлен своими руками от начала до конца, то ему однозначно необходимо вывести режущую кромку.
Процесс трудоёмкий, требующий внимания и точность руки. Но сегодня существует немало приспособлений, для упрощения этого действа.
Прогресс не стоит на месте. Механические приспособления позволяют закрепить клинок в одном положении и без опаски потери угла вывести режущую кромку.
Угол заточки
Важнейшим параметром является угол заточки. Изначально следует определиться в предназначении ножа. Для различных целей – угол свой, определяется суммарно с каждой стороны. Имея в виду 30° – угол с каждой стороны обязан равняться 15°.
Чем больше угол – тем надёжнее режущая кромка. Обычно для универсальных ножей достаточно 25°. Для рубки делают в районе 40°. Меньший угол заточки применяют в основном для кухонных ножей. Предназначение ножа, тесно связано с его режущей кромкой.
Слишком острая заточка.Нет необходимости затачивать мачете или топор под бритву – изделие не приобретёт нужных характеристик. И при первом ударе, затупится.
Полезные советы
Заточка ножей – это целая отдельная тема, в этой статье все нюансы не охватить. Но несколько советов, мы просто обязаны сообщить:
- не допускайте сильной потери остроты клинка, проще поправить режущую кромку, чем заново её создавать;
- проверить остроту несложно при помощи реза бумаги на весу, клинок должен шинковать её, а не мять или задирать;
- выправлению режущей кромки поможет закрашивание её маркёром, скользя по камню – будет видна затачиваемая поверхность;
- правильная заточка происходит от более крупного зерна камня к мелкому, займёт немало времени, но и результат будет на высоте.
Нет необходимости сильно давить клинком на брусок, процесс требует точности. При надавливании теряется контроль над углом заточки. Производить необходимо скользящие движения.
ПредыдущаяНожиКак сделать ножны для ножа своими руками
СледующаяНожиРукоять для ножа своими руками: инструкция по изготовлению
Набор ножей для резьбы по дереву своими руками
Всякий специалист прекрасно знает, как немаловажно иметь под руками хороший и надёжный инструмент.

Так получилось и со мной. Когда-то в беззаботном детстве я предпринимал попытки научиться резьбе по дереву. Для этих целей даже приобрёл набор резцов (изготовитель — «Запорожский инструментальный завод им. Войкова»). Многое из него потерялось к настоящему времени, но полукруглые стамески сохранились. К сожалению, попытки мои освоить резьбу в те времена не увенчались успехом — некому было показать основные приёмы работы с инструментом. Как результат — множество шрамов на левой руке и отбитое — почти буквально — желание совершенствоваться в этом направлении.
Этой осенью у меня возникло стремление наверстать упущенное. Благо появилось время — пришлось прекратить свои столярные экспромты в гараже и терпеливо ждать весны. Но теперь я решил начать с изготовления подходящего инструмента, и в первую очередь — ножей для резьбы по дереву. Одним из стимулов стало их отсутствие в местных магазинах.
Мои ножи (косяки и резаки) должны были удовлетворять следующим требованиям:
• высококачественная сталь, из которой они будут сделаны;
• эргономичные (удобные) рукоятки;
• относительная простота изготовления;
• надёжность.
Кроме того, я планировал взять для ножей те материалы, которые были в наличии.
Материалы и инструменты для изготовления ножей
В качестве исходного материала для изготовления клинков я использовал куски ленточной пилы. Ранее я из них делал кухонные ножи — они хорошо держат заточку.
Для рукояток я применял обрезки дубовых досок, оставшиеся от других работ. Дуб — прочный, красивый и технологичный материал.
Для работы мне потребовались электрическое точило, ленточная шлифовальная машинка (зернистость шкурки — 40), обычная ножовка, шлифовальная шкурка (зернистостью 80, а для доводки — 240, 800 и 1000), респиратор (марлевая маска) — для защиты органов дыхания.
Все детали склеивал столярным клеем «Titebond II».
Изготовление клинка
Из кусков полотна пилы длиной около 8 см я выточил металлические заготовки клинков нужной формы. У заготовок оставлял хвостовики длиной примерно 4,5-5 см. Такие их размеры обеспечивают достаточную прочность крепления клинка в рукоятке. Для более надёжной фиксации (чтобы нож не расшатался и не выпал из рукоятки) по бокам хвостовика сделал полукруглые вырезы.
Сечение клинка ножа обычно имеет клиновидное сужение (приблизительно под углом 10-15°) от обуха к режущей кромке. Это так называемая большая фаска или спуск клинка. Сама режущая кромка формируется малой фаской (подводом) — более крутым сужением (под углом 25-30°) в непосредственной близости от лезвия клинка.
Большую фаску на ножах я делаю до того, как вклеиваю хвостовик в рукоятку. При формировании фаски обтачиваю заготовку с двух боковых сторон под нужным углом. При этом стараюсь стачивать металл симметрично.
Самое главное в этой работе — не спешить. При интенсивном обтачивании металл нагревается, и происходит его отпуск. То есть металл становится более мягким и теряет способность сохранять заточку. Кроме того, обтачиваемую заготовку я время от времени охлаждаю в воде, не допуская её перегрева. Для этого рядом ставлю ёмкость с холодной водой и периодически опускаю в неё заготовку. Окончательное формирование лезвия, заточку и полировку произвожу уже на готовом ноже.
Изготовление рукоятки ножа
Для рукоятки подошли дубовые брусочки сечением 12×22 мм и длиной чуть больше 12 см. Бруски подбирал так, чтобы склеиваемые поверхности были ровными. Для упрощения работы гнездо под хвостовик выбирал в одной из половинок будущей рукоятки.
Последовательность операций такова. Хвостовик обрабатывал шлифовальной шкуркой по краям (сбивал заусенцы). После этого, прикладывая хвостовик к заранее подготовленному брусочку, обводил его карандашом или ручкой. Затем стамесками выбирал гнездо на глубину, равную толщине заготовки, время от времени собирая всю конструкцию «насухо», чтобы проверить, как брусочки прилегают друг к другу. Если глубина гнезда недостаточна, рукоятка не склеится либо склеится некачественно, и ручка во время работы может расколоться. В то же время при слишком глубоком гнезде клинок будет гулять из стороны в сторону, что также чревато нежелательными последствиями — растрескиванием рукоятки или деформацией хвостовика. Таким образом, необходимо выбрать гнездо под хвостовик максимально точно. Знаю это по собственному опыту — неоднократно приходилось раскалывать уже сделанные рукоятки кухонных ножей и менять на новые только из-за того, что хвостовики держались неплотно!
После того как при контрольной сборке «насухо» всех деталей был получен требуемый результат (плотная посадка хвостовика и отсутствие щелей между брусками-половинками рукоятки), можно приступать к склеиванию. Клей наносил на поверхность бруска и в гнездо под хвостовик — при ручной выборке гнезда неточностей по глубине не избежать, и возможные полости лучше заполнить клеем, который при высыхании затвердеет и будет удерживать хвостовик. На ответную деталь будущей рукоятки также наносил слой клея, но уже более тонкий.
Затем совмещал детали (необходимо максимально точно соединить торцы брусочков, расположенных ближе к клинку) и стягивал их струбцинами. Старался стянуть как можно сильнее, но, как говорится, без фанатизма, чтобы не расколоть бруски. Выдавленные излишки клея убирал влажной тряпкой и оставлял заготовку примерно на 12 часов до полного высыхания клея.
После этого я проверял плотность посадки хвостовика в рукоятке: одной рукой держал рукоятку, а второй пытался расшатывать клинок. Если при этом слышались едва уловимые тихие скрипящие звуки, то такая рукоятка никуда не годится, и её необходимо переделывать. При качественно выполненной работе никаких посторонних звуков быть не должно.
Подгонка рукоятки
Для себя я уже давно определил наиболее подходящие формы рукояток для режущего инструмента. Например, на рукоятках кухонных ножей и ножей для резьбы я обычно делаю небольшой изгиб на спинке для упора большого пальца.

• задняя часть рукоятки — более широкая и округлая, чем та, что ближе к клинку, поэтому все заготовки для рукояток в начале обработки напоминают усечённую вытянутую пирамиду;
• на рукоятке имеется выемка под указательный палец.
Когда заготовка склеена, ножовкой или торцовочной пилой отпиливаю заднюю часть, исходя из необходимых размеров (в моём случае — 12 см).
После этого перехожу к обтачиванию граней рукоятки ленточной шлифовальной машинкой. Работаю, используя средства индивидуальной защиты — защитные очки и респиратор, поскольку дубовая пыль может вызвать аллергию.
Не стоит стремиться выточить рукоятку инструмента максимально точно на ленте зернистостью 40. Лучше оставить небольшие припуски для более точной обработки мелкой шкуркой вручную. Подготовленные рукоятки я всегда покрываю нитролаком (он мне больше нравится).
Доводка клинка
Вернёмся к вопросу формирования режущей кромки. Угол заточки большой фаски в 10-15° годится, возможно, для опасной бритвы, но для ножа по дереву (пусть даже и самому мягкому) всё-таки мал. При обработке деревянной заготовки таким ножом остриё будет сминаться или скалываться. Поэтому и нужна малая фаска, угол заточки которой составляет для моих ножей примерно 25-30°. Для формирования малой фаски я использую шлифовальную шкурку (но можно и бруски) разной зернистости по принципу от большего к меньшему. Сначала я беру шкурку зернистостью 240, потом — 800, потом — 1000 и окончательно полирую на кожаном ремне, зафиксированном на деревянном бруске.
При хорошей заточке древесина должна резаться как вдоль, так и поперёк волокон без больших усилий. А поверхность среза должна быть ровной и блестящей — в этом случае говорят, что получается «масляный» рез.
Качество заточки проверяю на доске, специально используемой для этих целей. Доску беру из мягкой породы дерева, так как добиться «масляного» реза на такой доске труднее, чем на заготовках из твёрдых пород.
Естественно, в процессе резьбы нож тупится, и приходится время от времени восстанавливать режущую кромку. Я делаю это следующим образом: на ровный деревянный брусок накладываю лист шлифовальной шкурки и выполняю несколько притирочных движений, после чего довожу нож на ремне.
Действуя по описанной схеме, я изготовил за осень несколько ножей. Они вполне функциональны — надёжны и удобны. Для новичка, думаю, неплохо! Полученный опыт планирую использовать для расширения коллекции своего инструмента. Надеюсь, ножи станут моими верными помощниками при освоении резьбы по дереву.
Ножи для резьбы по дереву своими руками: последовательность робот
1. В качестве заготовки для изготовления клинков ножей использовал полотно ленточной пилы.
2. Хвостовики у всех клинков имеют приблизительно одинаковую форму.
3. В половинке будущей рукоятки стамесками выбрано гнездо для хвостовика.
4. Клей нанесён и на склеиваемую поверхность детали рукоятки, и хвостовик в гнезде. Чтобы не испачкать клеем столешницу, проще всего застелить её газетой.
5. При склеивании рукоятки детали стянуты струбцинами.
7. Этим рукояткам ещё предстоит придать нужную форму.
8. Первый этап обработки рукояток — обтачивание на ленточной шлифовальной машинке.
9. Рукоятки после грубой обработки.
10. Рукоятки обработаны мелкой шлифовальной шкуркой и подготовлены для нанесения лака.
Вот такой набор ножей для резьбы по дереву теперь есть у меня.
Ножи для резьбы по дереву видео
Как сделать резцы по дереву своими руками
Одна из самых актуальных тем для любого резчика -где взять хороший инструмент по дереву? Качественные хорошо заточенные резцы по дереву могут выручить даже не совсем опытного мастера.
Они достаточно хрупкие и прочные одновременно. Углеродистая сталь позволяет долго держать кромку лезвия острой, она не тупится даже о твердые породы дерева.
Итак, вначале разрезаем фрезу на резаке по металлу по заранее нанесенному рисунку будущего резака.
В нашем случае это маленький нож-резак, который является основным инструментом резчика.
Наличие такого обилия искр при резке говорит о том, что сталь хорошая, углеродистая, значит годится для резьбы по дереву.
Получается такая заготовка.
Желательно, чтобы та часть, которая будет в ручке была больше лезвия. Это для прочности.
Отшлифовываем лезвие ножа, постоянно окуная его в холодную воду, чтобы не перекалилось.
Теперь необходимо сделать ручку для ножа. Для этого берем реечки из прочной породы дерева. В одной части рисуем контур ножа, другая как накладка.
Вырезаем выемку в дереве по форме ножа, чтобы он утопился заподлицо, промазываем клеем Пва обе части.
Склеиваем нож в тисках. На склеивание уходит часов 12- сутки.
После склейки отшлифовываем ручку, а нож доводим на точиле до нужной остроты.
По такому принципу можно изготовить нож своими руками.
Кстати, отличные стамески по дереву получаются из сверел по металлу.
А полукруглые стамески из пробойников.
Нож – косяк можно изготовить из рапитовой пилы.
Вот еще резцы по дереву, которые я сделал своими руками из фрезы по металлу.
« Предыдущая запись Следующая запись »
Инструмент для резьбы по дереву своими руками: стамеска, резцы и ножи
Процесс резьбы по дереву, это захватывающее увлечение.
Для начального уровня хватит нескольких приспособлений, которыми можно наносить рисунок на деревянную поверхность. В этой статье пойдет речь о том, как изготовить первые наборы для резьбы по дереву. Для начала следует определиться, какие инструменты по дереву для начинающих вам понадобятся.
Стамески
Стамески для резьбы по дереву своими руками изготовить можно, имея в наличии заготовку из металла и болгарку с заточным камнем. Окончательная заточка стамесок производится вручную, без применения электроинструмента, после придания нужной формы острию необходимо закалить его.
Закаливать режущую часть стамески надо после придания формы и заточки острия. Для этого нагрейте острую часть инструмента до малинового цвета при помощи газовой или керосиновой горелки и опустите в емкость с машинным маслом или отработкой.
Совет! Сразу после помещения рабочей части стамески в жидкость, переместите ее в песок, это избавит вас от процедуры очищения стамески от мазута.
Острие у стамески бывает прямым и фигурным, проще всего в изготовлении прямое острие, что бы сделать правильную фигурную стамеску необходимо знать пропорции.
Ручку можно выточить на домашнем токарном станке, собранном из двигателя от старого холодильника и уголка разного размера.
Виды стамесок для резьбы по дереву имеют разную размерность и форму рабочей части, она выражается в числовых значениях от 1 до 12.
Кривизну стамески определяет цифра ей присвоенная, чем она ровнее, тем меньше числовое значение используется для ее обозначения. Ровные стамески для резьбы по древу используются в основном на начальной стадии обработки заготовки. Более кривые V и U образные, которым присвоены номера 12 и 11 соответственно применяются для придания окончательного внешнего вида изделию.
Совет! При изготовлении рукояти под стамеску старайтесь сделать ее более плоской формы, это предотвратит непроизвольное скатывание инструмента со стола. При падении на рабочую часть она тупится и требует частой заточки.
Резьба по дереву производится небольшими стамесками, размером с ладонь взрослого человека. Существуют инструменты меньшего размера, их применяют в работе с мелкими деталями.
Резцы
Один из наиболее часто используемых инструментов для резьбы по дереву это резак. Резцы для резьбы по дереву должны быть разнообразной формы, всего в комплект входит от шести разновидностей. Виды резцов по дереву зависят от нижеописанных факторов.
Отличием служит форма лезвия и угол его наклона, в зависимости от них резец выбирается для каждого конкретного случая. Из шести приборов один обычно считается основным, большая часть операций выполняется с его использованием. Вот некоторые требования применимые ко всем разновидностям резцов:
- Удобство – рукоятка должна хорошо лежать в ладони, и не иметь острых краев, что бы в процессе работы не повредить руку;
- Острота – лезвие должно всегда быть хорошо наточено. Что бы заточка держалась дольше, лезвие выполняется из легированной инструментальной стали.
Заточка резцов процесс ответственный и сложный, так как порой они имеют причудливую форму лезвия.
Покупая резец на рынке или в специализированном магазине, не постесняйтесь взять его в руки и проверить, удобно ли вам будет с ним работать в дальнейшем.
Ножи
В работе с деревом не обойтись без хорошего ножа, выбирая этот инструмент, следует отдавать предпочтение тому, который будет наиболее удобным в обработке древесины. Так же немаловажно узнать какая марка стали использовалась при его изготовлении.
Выбирая нож от зарубежного производителя необходимо сопоставить указанную марку стали с отечественным аналогом, и проверить какими свойствами она обладает согласно марочнику сталей.
Для хорошего ножа характерно высокое содержание углерода с добавлением легирующих элементов.
Ножи для работы с деревом делятся на три вида складные, со сменным и фиксированным лезвием. Оптимальным считается лезвие длиной от 40 до 50 мм и толщиной в 4 мм.
Электроинструмент
Резьба по дереву предполагает ручную обработку, но на начальном этапе допускается использовать электроинструменты для резьбы по дереву. В их число входят:
- Электрический лобзик;
- Дрель;
- Токарный станок;
- Электрорубанок.
Подготовительные этапы, предусматривающие дополнительное оборудование нужны для придания заготовке необходимых пропорций для дальнейшей обработки при помощи ручных инструментов.
Мастерская любителей резьбы по дереву должна быть оснащена стандартным набором электроинструментов.
Изготовление ножа
Вариантов самостоятельного изготовления ножей существует огромное множество, рассмотрим самый популярный из них.
Нож из полотна от ножовки по металлу
Для такого ножика подойдет поломанное или сточенное полотно. Процесс его обработки довольно сложен, это объясняется высоким качеством стали, но с другой стороны тем лучше получится инструмент.
При помощи болгарки разрежьте полотно на три части, под углом в 45 градусов, этот угол будет рабочей поверхностью будущего ножа.
Болгарка при работе разгоняется до высоких оборотов, что повлияет на качество металла, все легирующие элементы вблизи пропила просто выгорят. Поэтому после распиливания потребуется зажать нужную часть полотна в тиски и при помощи напильника снять два, три испорченных миллиметра.
Если полотно слишком толстое, то мелким напильником или надфилем рекомендуется снять излишки металла. Заточка инструмента для резьбы по дереву требует основательного подхода, для этого потребуется надфиль и наждачная бумага.
Когда заточенный резец готов можно подумать о рукояти. Самым простым будет просто обмотать ее изолентой или сырой резиной, но профессионалы предпочитают ручки из древесины.
Видео: самодельные инструменты для резьбы по дереву
Какие Заточные станки для ножей: виды, советы по выбору, изготовление своими руками- Обзор +Видео
Заточка ножей – процесс, с которым способны справиться даже нежные женские руки. Ведь в наше время существует множество приспособлений, облегчающих эту задачу. Керамические ножи, к примеру, не требуют затачивания, что очень удобно, а ножи из стали требуют периодической заточки, поскольку материал тупится. Для придания остроты ножам, можно воспользоваться брусками с абразивным покрытием или заточным станком для ножей.
Последний метод требует соблюдения рекомендаций специалистов, тогда и результат вас непременно порадует.
Инструменты для заточки ножей
- Брусок точильный.
- Напильники со специальной насечкой.
- Приспособления для наточки.
- Станки для заточки ножей.
Примечание.
Заточка ножей по старинке, конечно, хороший и действенный способ, но точно настроенный станок для бытового использования дает более качественный результат с нужным углом формирования кромки лезвия.
Правила заточки ножей
Специалисты рекомендуют соблюдать ряд правил, для того, чтобы получить качественную заточку ножей в домашних условиях, что в свою очередь позволит сократить количество заточек лезвия.
Если вы сторонник использования бруска с абразивным напылением, начинайте работу с самой острой части лезвия, и заканчивайте более тупой, а именно той, которая мало задействована в процессе нарезки продуктов. Зачастую процесс начинают с середины, двигаясь к острию лезвия с небольшим поворотом. Форма ножа и его толщина влияет на угол заточки лезвия. Заточной станок для кухонных ножей выполняет точение под углом 25°, лезвие наклоняют над бруском на 12 — 13°.
Тип заточного станка для ножей рейсмуса и материал, из которого он изготовлен, также влияет на качество проведения работы.
На различных интернет ресурсах, вы можете найти специальные видео ролики, в которых наглядно показан процесс заточки лезвия ножа.
Примечание.
Производство ножей происходит в основном из легированной и углеродистой стали. Каленую сталь нужно точить бруском с абразивом, нержавейку – напильником трехгранным. Это связано с тем, что относительно мягкие металлы, в процесс заточки забывают поверхность бруска с абразивом. Кованое лезвие довольно гибкое, поэтому его желательно закреплять и точить бруском движениями вскользь. Частое применение абразивных брусков, способствует образованию жирной пленки на поверхности, которую нужно затирать обдиркой.
Раньше, станки заточные настольные для ножей делали из брусков клиновидной формы и дуба мореного. Бруски располагали с обеих сторон деревянного клинка, таким образом, чтобы кромка режущая была свободной. Конструкцию перетягивали веревкой и при помощи точильного камня затачивали лезвия до предельной остроты, получая при этом, отличный угол заточки.
Затачивание ножей, которые используются в рубанках, выполняется следующим образом: на стекло большой толщины, накладывают наждачную шкурку с мелкой фракцией, скошенной частью кромки режущей на абразив и точится движениями по кругу.
Заточка ножей в домашних условиях
Для этой цели потребуется взять брусок из твердых пород дерева, поверхность которого формируют методом заточки под определенным углом, необходимым для формирования кромки лезвия. Это дает возможность держать угол обрабатываемой кромки. Для удобства работы по заточке лезвия, зафиксируйте клинок в плоскости бруска при помощи саморезов.
Заточный станок для ножей фуганка изготовьте инструмент своими руками, это даст возможность сделать процесс более легким, а качество работы намного выше. Главное соблюдать правила и нюансы в работе, и проблем не возникнет.
Заточный станок для ножей своими руками создан для облегчения работы с металлическими изделиями. Домашний инструмент можно наточить своими руками при помощи подручных средств, а на производстве без станка не обойтись. Там и объемы больше, и инструментарий посерьезней.
Профессиональные заточные станки для ножей
Самыми острым инструментом считается обвальный или разделочный нож
Таким пользуются мясники для разделки туш животных, и срезания шкур. При такой интенсивной работе лезвие инструмента тупится чрезвычайно быстро. Если объем работы не слишком большой, заточку можно производить на обычном станке, который оснащен контролем над углом кромки лезвия. Заточные станки для ножей в мясоперерабатывающей промышленности используют в основном KNECHT USK 160. Такие станки универсальны, поэтому затачивать на них можно абсолютно любые ножи.
На предприятиях занимающихся деревообработкой и в столярных цехах, устанавливают оборудование, которое может справляться с большими объёмами работ. Здесь используется инструмент, имеющий фуганки с длинными лезвиями, а также строгальные станки. Заточка металла происходит на оборудовании с механическим приводом, который подает инструмент на заточку.
При попытке заточки инструмента самостоятельно при помощи точильной чаши
…без использования фиксации и направляющих, то на лезвии сформируются зоны с разнообразным углом отточки. Обрабатывая некачественно заточенным инструментом дерево, вы получите неровный срез и волнистую поверхность. Заточной станок для плоских ножей имеет простую вертикальную конструкцию, Диски точат на станках с разделителем и вращающимся столом.
Универсальный заточной станок для ножей
Данный вид оборудования наилучшим способом подходит для предприятий, который выполняют за день большие объемы работ. Вручную возиться з металлом никто не станет, поскольку это тяжелый труд. Настольный станок ВЗ-319 оборудован жесткой станиной и точно подогнанными механическим приводом. Поэтому, справляется с заточкой инструмента любого типа – рубанки, фрезы, ножи и прочее.
Для бытового использования подойдет модель Тормек Т7. Комплектация у данного агрегата большая, в наличии есть множество насадок и дополнительных элементов для заточки кухонных ножей, ножниц и прочих инструментов.
Изготовление заточного станка для ножей своими руками
Сделать заточной станок для ножей для бытового использования довольно просто, для этого вам понадобится отрезок ламината, фанеры или ДСП, деревянная рейка, наждачка, болты с барашками. Первым делом нужно изготовить держатель ножа, для этой цели отрежьте кусок материала. Во избежание цепляния бруска за держатель, нужно провести зачистку края под определенным углом при помощи наждака. На вертикальной стойке сделайте разметку и отрежьте верх, это послужит основой для бруска. Угол устанавливается вдвое меньше, необходимого для заточки лезвия.
Для бытовых ножей угол составляет 10 — 15°. Для облегчения работы по сооружению станка для заточки ножей, сделайте чертеж, так вам будет намного проще. Возьмите во внимание тот факт, что на высоту влияет поперечная основа.
На конечном этапе, все элементы нужно обрезать и зашкурить. Затем, необходимо сделать дырки для болтов в пластине, которые будут фиксировать лезвие. Делая разметку, определяйте расстояние дырок от края основы. Это позволит затачивать лезвия разной толщины.
На следующем этапе, пластину нужно закрепить с использованием болтов. Стойки вертикального положения фиксируют при помощи шурупов. Важно помнить о том, что сила давления на низ малая, поэтому для фиксации элементов можно применить термический клей. Горизонтальную перекладину крепят аналогично.
Для изготовления бруска нужно отрезать рейку определенной длины. На одном краю крепят наждачку с достаточной фракцией абразивных частиц. Для того, чтобы добиться лучшего результат в работе, можно сделать больше брусков с разным абразивом. Хорошим диапазоном зернистости считается Р600 – Р2000.
Примечание.
Для того, чтобы защитить руки от травм при заточке инструмента, прикрутите на верху рейки рукоятку. Таким образом, вы получите станок для домашнего использования с хорошими функциональными качествами.
В процессе работы по заточке ножей, устройство получает опору на столе, что в свою очередь облегчает работу с ним.
Ковка ножа своими руками | Строительный портал
Сегодня, даже при таком большом ассортименте различных ножей прекрасного качества от известных производителей, ножи ручной ковки по-прежнему пользуются особой популярностью. Это и неудивительно, так как такие ножи обладают особой энергетикой и привлекательностью. А если сам клинок сделан из легированной стали и со знанием дела, то такой нож бесценен. Из различных способов собственноручного изготовления ножа наиболее трудоемким является ковка ножа своими руками. Следует отметить тот факт, что ковка ножа позволяет создать наиболее прочный и качественный клинок, который прослужит не один десяток лет и при этом сохранит свои качества. Ковка ножа своими руками – дело, требующее от мастера высокого уровня навыков владения инструментом, знания металлов и их свойств. Для тех, кто решил выковать нож впервые, описанные ниже рекомендации помогут сделать свой первый клинок.
- Как выбрать сталь для ножа
- Инструмент для ковки ножа
- Конструкция ножа
- Ковка ножа из сверла
- Ковка ножа из подшипника
- Ковка ножа из рессоры
- Ковка ножа из напильника
- Ковка ножа из троса
- Закалка и отпуск клинка
Как выбрать сталь для ножа
Качественный самодельный нож отличает правильный подбор стали для него, от этого будут зависеть режущие и прочностные характеристики самого ножа. Чтобы правильно подобрать сталь, необходимо знать и понимать, какими свойствами обладает сама сталь. Для ковки ножа своими руками нужно ориентироваться на пять основных свойств стали – устойчивость к износу, твердость, прочность, вязкость, красностойкость.
Твердость – это свойство стали, указывающее на её способность сопротивляться проникновению в неё другого более твердого материала. Говоря проще, твердая сталь лучше сопротивляется деформации. Сам показатель твердости измеряется по шкале Роквела и имеет показатель от 20 до 67 HRC.
Устойчивость к износу – сопротивление материала изнашиванию в процессе эксплуатации. Это свойство напрямую зависит от твердости самой стали.
Прочность указывает на способность сохранять целостность под воздействием различных внешних сил. Проверить прочность можно на изгиб или при сильном ударе.
Пластичность – способность стали поглощать и рассеивать кинетическую энергию во время удара и деформации.
Красностойкость – это показатель, отвечающий за устойчивость стали к температурам и сохранению её изначальных качеств при нагреве. От того насколько сталь устойчива к термообработке, зависит минимальный показатель температуры, при котором её можно ковать. Самыми красностойкими сталями являются твердые марки, рабочая температура ковки для которых более 900 °C. При этом необходимо отметить, что температура плавления стали составляет 1450 – 1520 °C.
Все эти свойства связаны между собой и преобладание одного из них ведет к ухудшению другого. При этом то или иное свойство стали зависит от содержания в ней различных легирующих элементов и добавок, таких как кремний, углерод, хром, ванадий, вольфрам, кобальт, никель, молибден.
Наличие тех или иных легирующих элементов и их пропорциональное использование при изготовлении стали, знание свойств, которые придают легирующие элементы и добавки, позволило создавать сталь для определенных целей и нужд. Такие стали имеют каждая свою маркировку. При этом отечественные и зарубежные марки стали обозначаются по-разному. Для удобства в марке стали указан основной состав одного или нескольких легирующих элементов. Например, сталь марки У9 говорит о содержании в ней углерода в десятых долях процента. Аналогом стали марки «У» являются стали 10хх, где «хх» – это содержание углерода. И чем меньше значение, тем меньше его содержание. Или такая сталь как Х12МФ указывает на высокое содержание хрома и молибдена, что говорит о нержавеющих и высокопрочностных свойствах стали.
К отечественным маркам, которые часто используются при ковке ножей в домашних условиях, относятся все стали с маркировкой от У7 до У16, ШХ15, 65Г, Р6М5, Х12МФ. Из зарубежных аналогов можно выделить сталь O-1, 1095, 52100, M-2, A-2, 440C, AUS, ATS-34, D-2. Каждая их вышеприведенных марок используется в изготовлении ножей, различного инструмента и запчастей. Например, марки стали Р6М5, У7-У13, 65Г применяют для производства сверел, буров, тросов, рессор, подшипников, напильников. Поэтому именно из этих предметов народные умельцы делают ножи ручной ковки.
Конечно, можно найти и другие изделия из той или иной стали. Для этого достаточно будет прочитать полное описание марки стали и её применение в Марочнике Стали и Сплавов, а потом использовать изделие из неё для ковки ножа.
Инструмент для ковки ножа
Для ковки ножа потребуется определенный инструмент кузнеца, который можно приобрести в магазине. Но можно использовать и непрофессиональный инструмент:
- молот на 3 – 4 кг и молоток меньшего веса до 1 кг;
- кузнеческие щипцы или обычные пассатижи, но без изоляции на ручках, а также разводной ключ;
- тиски;
- наковальня или её самодельный аналог из двутавра;
- болгарка и сварочный аппарат;
- точильный станок;
- печь.
Если с обычным инструментом все более-менее понятно, то по поводу печи необходимо сделать некоторые пояснения. Все дело в том, что в обычном очаге сложно получить температуру более 900 °С. Да и греться заготовка там будет целую вечность. Поэтому необходимо немного усовершенствовать очаг. Если ранее Вы не занимались хотя бы закалкой металла, то придется сделать с нуля небольшую печь из толстостенного металла. Затем присоединить к ней трубу, по которой будет поступать воздух при помощи вентилятора или старого пылесоса. Таким нехитрым образом можно получить достаточно надежное горнило для доведения заготовок до температуры 900 – 1200 °С. В качестве топлива используется обычный древесный уголь, желательно такой, который дает как можно больше жару и горит подольше.
Конструкция ножа
Прежде чем приступить к самим работам, необходимо сделать эскиз самого ножа.
По сути, нож довольно простой предмет, состоящий из клинка и рукоятки. Но вот каждый из этих элементов имеет целый набор составляющих. На демонстрирующем конструкцию ножа фото можно увидеть все элементы ножа и как они называются.
Также необходимо знать и о некоторых основных профилях клинков, чтобы сделать наиболее подходящий эскиз. На фото ниже приведены профили ножей.
Выбрав наиболее подходящий для Вас профиль, можно смело приниматься за создание эскиза. Конечно, опытные мастера обходятся без зарисовки, но для новичка все же важно сделать эскиз и держать его перед глазами в процессе ковки.
Ковка ножа из сверла
Сверла получили большую популярность при ковке ножей благодаря используемой в них легированной стали Р6М5, которая отличается прочностью, легкостью заточки и износоустойчивостью.
При выборе сверла для ковки следует отметить один важный момент. Большие сверла состоят из рабочей спиралевидной части из Р6М5 и хвостовика из обычной стали. Маленькие сверла обычно полностью из Р6М5. При ковке ножа из большого сверла необходимо сразу определить, где какая сталь и где между ними граница. Сделать это можно достаточно просто, всего лишь немного проточив сверло по всей длине. Там, где обычная сталь, сноп искр будет большой и желто-оранжевого оттенка. А вот там, где легированная сталь, сноп будет реденьким и ближе к красноватому оттенку. Описанная выше процедура необходима для того, чтобы определить, где у ножа будет начинаться клинок, а где хвостовик. Закончив с этим, переходим к самой ковке.
Вначале разводим огонь в печи, подключаем поддув и ждем, когда угли разгорятся достаточно сильно, после чего помещаем сверло в горнило. Но делаем это с помощью клещей и так, чтобы хвостовик большей частью оставался вне огня.
Важно! Выполняя ковку ножа впервые, можно не сразу определить, когда металл нагрелся до необходимой температуры. Вследствие чего можно испортить не одно сверло. Поэтому прежде чем браться за ковку сверла, можно немного потренироваться с нагревом и ковкой металла на обычной арматуре. При этом необходимо запоминать, какого цвета был металл и когда он ковался наиболее мягко.
Также стоит помнить о том, что на солнечном свете даже нагретый до 1100 °С металл будет выглядеть темным.
Как только сверло нагреется до необходимой температуры, а это более 1000 °С, его сразу же необходимо вынуть из горнила, и зажать низ хвостовика в тисках. После чего взять разводной ключ, зажать им верхушку сверла и сделать круговое движение, расправляя спираль. Делать все необходимо быстро, чтобы металл не успел остыть, иначе рискуете сломать сверло. Если не получилось сделать это за один раз, ничего страшного. Просто повторно раскалите сверло и повторите процедуру. В результате должна получиться относительно ровная полоска металла.
Следующим шагом будет ковка сверла и раскатка металла до приемлемой толщины. Тут все довольно просто. Раскалив металл до необходимой температуры, берем тяжелый молот и начинаем сильными, но равномерными ударами ровнять металл и придавать ему ровную форму. В результате должна получиться полоска металла толщиной около 4 – 5 мм.
Важно! При ковке металла необходимо постоянно следить за цветом заготовки. Как только она начала тускнеть, приобретая вишневый цвет, её сразу же возвращаем в горн. Лучше лишний раз накалить металл, чем сломать его под ударом молота.
Далее выковывается острие ножа. Тут все несколько сложнее. Дело в том, что необходимо придать заокругленную форму и при этом сохранить необходимую толщину лезвия. Вся работа практически ювелирная и потребует определенной ловкости. Ковка выполняется таким образом, чтобы постепенно заокругливая острие, понемногу оттягивалось лезвие в длину. Удары должны быть сильные, но аккуратные. У новичка может не получиться с первого раза, но немного практики все исправит.
Следующим шагом будет проковка режущей кромки ножа. Это довольно важный и сложный этап. Для этого потребуется более легкий молот и желательно с заокругленным бойком. Начиная с середины лезвия, постепенно сдвигаем металл вниз к режущей кромке. Стараемся сделать режущую кромку как можно тоньше. При этом следим, чтобы само лезвие оставалось прямым и ровным. Удары наносим очень аккуратно и стараемся прилагать лишь столько усилий, сколько требуется для небольшой деформации раскаленного металла. Помним о цвете заготовки и при необходимости отправляем её обратно в горнило.
После того как удалось выковать лезвие и острие, переходим к проковке хвостовика. Сами работы будут намного проще, чем при выковке лезвия. Вначале накаливаем круглый хвостовик сверла и затем раскатываем его сильными ударами молота. В зависимости от эскиза хвостовик может быть как узким, так и широким. Тут уже кому как нравится делать ручку ножа. Кто-то делает простые накладки, а кто-то делает наборную рукоятку.
По завершению ковки даем металлу постепенно остыть и затем переходим к шлифовке. На шлифовальном станке снимаем лишние слои металла и неровности, делая нож идеально ровным и блестящим. При шлифовке может уйти до 2 мм толщины, и нож станет намного легче и тоньше. Также на этом этапе можно выполнить заточку ножа. Напоследок выполняем закалку ножа. О том, как это делается, будет написано ниже.
Ковка ножа из сверла видео-обзор:
Ковка ножа из подшипника
Еще одним популярным материалом для ковки ножей является подшипник, а именно его внутренний или внешний обод. Причем внутренний даже предпочтительней. Все работы по ковке ножа из подшипника практически идентичны ковке из сверла. За некоторым исключением.
Во-первых, заготовку из ободка подшипника вырезаем при помощи болгарки. Длину стараемся взять с запасом, так чтобы и на нож хватило и еще 1 – 2 см осталось. Во-вторых, на начальной стадии ковки вырезанную заготовку следует приварить к прутку арматуры. И в таком виде накалять и ковать. В-третьих, если в случае со сверлом заготовку раскатывали из круглой в плоскую, то для обоймы подшипника её необходимо просто выровнять. А дальнейшие действия по ковке самого клинка и хвостовика полностью аналогичны. Единственное, что стоит отметить, – из подшипника все же удобнее делать нож с накладными рукоятками.
Ковка ножа из подшипника видео-обзор:
Ковка ножа из рессоры
В поисках подходящей стали для качественного ножа многие используют рессору. Металл этой автомобильной запчасти отличается высокой упругостью и долговечностью, что делает его прекрасным образцом для ножей ручной ковки. Справедливости ради, необходимо отметить, что нож из рессоры можно изготовить и обычным вырезанием профиля ножа с дальнейшей заточкой и закалкой. Но все же, чтобы нож был действительно надежным, его лучше проковать, тем более что толщина рессоры достаточно велика, а для хорошего ножа её следует уменьшить.
Ковку ножа из рессоры начинаем с зачистки болгаркой от ржавчины и разметки пластины. Потребуется лишь небольшая часть рессоры, поэтому отметив её, отрезаем при помощи болгарки. Далее привариваем заготовку к арматуре и накаляем её. После чего постепенно проковываем, доводя до необходимой толщины. Выковываем острие и режущую кромку, как это делать, описано выше на примере ковки ножа из сверла. Добившись желаемого, оставляем нож постепенно остывать и затем шлифуем и затачиваем его.
Ковка ножа из рессоры видео-обзор:
Ковка ножа из напильника
Износостойкую и прочную сталь можно найти в различном слесарном инструменте и напильник тому яркий пример. Изготовление ножей из напильника достаточно популярное занятие. Тем более что клинки получаются на редкость долговечными с прекрасной режущей кромкой. Но ковка ножа из напильника имеет свои особенности.
Прежде всего, потребуется очистить напильник от насечек и возможной ржавчины. Сделать это можно с помощью болгарки. Далее при необходимости отрезаем от напильника заготовку необходимой длины. После чего привариваем её к куску арматуры и засовываем в горнило. Накалив заготовку до нужной температуры, приступаем к раскатке заготовки до необходимой нам толщины. Затем делаем острие и режущую кромку. Хвостовик ножа из напильника лучше всего сделать под накладную ручку.
Ковка ножа из напильника видео-обзор:
Ковка ножа из троса
Изготовление ножа из стального троса довольно редкое явление. Так как в отличие от всех описанных выше заготовок, трос представляет собой разрозненные волокна проволоки, и ковать их довольно сложно. К тому же сталь троса не обладает такими высокими характеристиками, как сталь сверла или напильника. В большинстве своем ножи из троса куют из-за их необычного рисунка на клине, отдаленно напоминающего дамасскую сталь. Для того чтобы сделать такой нож, необходимо приложить несколько больше усилий, чем при ковке из обычного бруска стали.
Ковка ножа из троса начинается, как и обычная ковка. Вот только есть несколько маленьких секретов. Во-первых, это касается хвостовика. Многие мастера делают хвостовик ножа из троса в виде готовой рукоятки. Смотрится это весьма необычно и красиво. И тут есть два подхода в изготовлении рукоятки. Взять толстый трос и затем сварить его конец, сделав монолитным куском. Или сделать рукоятку в форме петли, а из концов выковать клинок. Во-вторых, ковка троса – дело сложное из-за разрозненных проволок, из которых состоит трос. Чтобы сделать нож, потребуется их сварить между собой. А это целое искусство и рассчитывать, что нож из троса получится с первого раза, не стоит. Сварку можно выполнить двумя путями. Первый – проварить электросваркой вдоль больших канавок. Второй – выполнить кузнеческую сварку. Второй вариант сложнее и в то же время предпочтительней.
Итак, выбрав способ создания рукоятки, приступаем к ковке ножа. Для этого раскаливаем трос до ярко-красного цвета. Затем вынимаем его и посыпаем бурой. После чего вновь отправляем в горнило. Таким нехитрым образом выполняется подготовка к кузнеческой сварке. Бура представляет собой соль тетраборной кислоты и применяется мастерами для сварки отдельных слоев стали. По сути это флюс, который облегчает процесс плавки и предохраняет расплавленный металл от попадания кислорода и устраняет оксиды металла. Буру можно найти в свободном доступе без особых проблем.
После того как трос обработали бурой со всех сторон и он раскалился от 900 до 1200°С и более, вынимаем его из горнила и начинаем проковывать. Удары наносим тяжелым молотом, но при этом стараемся сохранить волокна троса вместе. Сложность ковки троса именно в этом. Но потренировавшись можно добиться приемлемых результатов. В конце концов, трос можно накалять и проковывать сколько угодно раз. Но при этом каждый раз, нагревая его в горне, посыпать трос бурой. В результате получится монолитный кусок стали, состоящий из множества слоев, почти как у дамасской стали. После чего остается лишь выковать клинок необходимой формы. На демонстрирующих ковку ножей видео уже не раз было показано, как именно делается раскатка клинка, создание режущей кромки и острия.
Закалка и отпуск клинка
Как уже отмечалось ранее, закалка ножа – это один из самых важных этапов его изготовления. Ведь именно от того насколько правильно была она выполнена, зависят рабочие характеристики ножа. Сам процесс закалки выполняется уже после того, как нож остыл и был отшлифован на точильном станке.
Закалка клинка начинается с его нагрева от светло-красного до оранжевого цвета. После чего нож опускается в воду или масло. При этом в воду добавляется 2 – 3 ложки поваренной соли на 1 л, а температура воды должна быть 18 – 25 °С, масла 25 – 30 °С. Закалка выполняется довольно быстро и чтобы все прошло удачно после закалки клинок необходимо отпустить. Сама закалка стали происходит в диапазоне температур от 750 до 550 °С. Момент закалки можно даже прочувствовать, когда сталь начинает «дрожать и стонать» в жидкости. Как только процесс заканчивается, клинок необходимо достать и дать ему остыть естественный образом.
Отпуск клинка выполняется уже после закалки. Сам процесс подразумевает ослабление внутреннего напряжения стали, что делает его более гибким и устойчивым к различного рода нагрузкам. Перед тем как сделать отпуск, клинок следует очистить от возможной окалины и затем вновь нагреть. Но температура при отпуске значительно меньше. Сам нож нужно уже держать над пламенем и наблюдать за ним. Как только вся поверхность покроется желто-оранжевой пленкой, убираем нож от огня и даем ему остыть естественным образом.
Иногда закалка и отпуск производятся при помощи масла или воды, а иногда через масло в воду. Такая закалка выполняется очень быстро. Сначала клинок опускается в масло на 2 – 3 секунды, а затем в воду. При таком подходе риск сделать закалку неправильно минимален.
Ковка ножа своими руками лишь кажется простой задачей. Кроме того что придется довольно много помахать кузнечным молотом, так еще и без опыта в вопросе ковки металла с первого раза может не получиться выковать нож. Поэтому сначала необходимо набить руку и немного потренироваться, а затем уже приступать к ковке ножа.
Изготовление ножей с помощью основных инструментов: 13 шагов (с изображениями)
Здесь вы можете пойти на супер-базовый уровень или использовать несколько электроинструментов.
Я пошел на базовый уровень, потому что был вынужден.
Инструменты
– Я купил угловую шлифовальную машину за 30 долларов r, чтобы выполнять большую часть работы по резке и формованию. Конечно, вы также можете использовать ножовку, но это большая работа. Для черновой резки я использовал металлический отрезной диск. Для профилирования лезвия я использовал подкладку с наждачной бумагой, показанной на рисунке.Покупайте их мелкой крупой, начиная с зернистости 60. Или вы можете просто получить несколько лепестковых дисков, как показано на рисунке.
– Напильники вам понадобятся разнообразные, от грубых до тонких, а также круглые или закругленные с одной стороны.
– Наждачная бумага Приобретите водостойкую наждачную бумагу различной зернистости от 120 до 1000.
– Зажимы У меня есть несколько быстрых зажимов и струбцина, чтобы удерживать нож во время работы.
– Drill Вы можете использовать ручную дрель, но это проще, если у вас есть сверлильный станок и несколько сверл для сверления стали
– Dremel Не обязательно, но они пригодятся для некоторых деталей шлифования.
– Решетка Для термообработки ножа
– Копировальная пила
Материалы
– Сталь Я купил кусок стали CRA 1095 у Admiral Steel 5/32 “X 1 1/4 “X 96” по цене менее 30 долларов с доставкой. Хорошая сталь для лезвия по такой цене. 5/32 “- красивый и толстый, хороший нож для выживания или охоты.
– Материал ручки Вы можете использовать тонну различных материалов для своей ручки; дерево, кость, микарта и даже рог.Я предпочитаю дерево, потому что по профессии я плотник и люблю его. Я купил кусок кокоболо для весов (материал ручки) в Owl Hardwoods, потому что я был поблизости по работе.
– Штифт Вы можете купить его в Интернете у поставщиков ножей или просто зайти в магазин Ace и просмотреть их пруток из латуни или нержавеющей стали. Обычно в разделе хобби. Я купил и то, и другое.
– Эпоксидная 30 мин. 2 тонны. Не пробуйте 4 мин. потому что вам может понадобиться немного рабочего времени.
– Льняное масло Вы можете использовать его для отделки деревянной ручки или можете нанести на нее немного полиуретана.
Инструменты, необходимые для создания цеха по изготовлению ножей
Изготовление ножей может быть как ремесленным, так и высоко автоматизированным процессом, но, как и в любом ремесле, есть несколько очень специфических инструментов, которые упрощают весь процесс. Хотя вы могли бы сделать нож из куска стали и пары напильников, наличие подходящих инструментов в вашем магазине значительно упростит задачу.
Создайте свою мастерскую по изготовлению ножей
Есть несколько видеороликов, в которых рассказывается об основных инструментах для изготовления ножей. Один из моих любимых произведений принадлежит владельцу Tormach Уолтеру Сорреллсу.
Он знакомит нас с рядом ценных инструментов, которые могут пригодиться в любом магазине, но особенно при изготовлении ножей. В его списке:
- Файлы
- Ножовка по металлу с биметаллическим полотном
- Тиски для скамьи
- Сверлильный пресс
- Наждачная бумага и абразивы
- Суппорт
- Зажимы сварочные и прочие разные
- Точильные камни
- Ленточно-шлифовальный станок
- Печь для термообработки
Этот список предназначен для новичков (которые, вероятно, имеют ограниченный бюджет), но если вы строите магазин, вы, вероятно, готовы более серьезно относиться к изготовлению ножей.Может быть, даже начать свой бизнес!
Мы связались с Уолтером, чтобы получить еще несколько советов и уловок для тех, кто хочет выйти за рамки новичков.
«Покупка приличной ленточно-шлифовальной машины – настоящий признак того, что вы серьезно относитесь к изготовлению ножей», – говорит он. «После того, как вы совершите этот прыжок, в вашем магазине волшебным образом начнут появляться множество небольших электроинструментов, таких как дисковые шлифовальные машины, роторные инструменты и абразивные пилы. Некоторые основные инструменты, такие как ленточные пилы и настольные пилы, также имеют очевидное применение в цехе по изготовлению ножей.”
Ленточно-шлифовальный станок, безусловно, является необходимым элементом, если вы серьезно относитесь к изготовлению ножей, но другие абразивные инструменты также могут быть весьма полезны. «Даже если вы профессиональный производитель нестандартных изделий, шлифовальный станок неоценим», – говорит Сорреллс. «Они снимают огромное количество рутинной работы, связанной с получением плоских вещей – будь то сплющивание кончиков кованых лезвий, обработка поверхности ножа для удаления припусков или удаление окалины с дамасской заготовки.”
Несмотря на то, что существует множество вариантов плоскошлифовальных машин, есть реальная ценность в добавлении немного автоматизации в процесс. «Ручные плоскошлифовальные станки – это хорошо, но автоматизированные плоскошлифовальные станки, такие как Tormach PSG 612, дают оператору небольшого магазина возможность выполнять две задачи одновременно. Однако, если вы купите 612, я настоятельно рекомендую приобрести ленточно-шлифовальный станок. Я обнаружил, что для изготовления моих ножей это работает лучше, чем использование шлифовальных кругов ».
Добавление ЧПУ в цех по изготовлению ножей
Добавление фрезерного станка (особенно с ЧПУ) к производству ножей не для всех, но у него определенно есть свои преимущества.«Большой скачок после покупки ленточно-шлифовального станка – покупка мельницы», – объясняет Сорреллс. «Мельницы – король металлообрабатывающего цеха. Они являются огромным умножителем силы для изготовителя ножей. Они помогают вам работать быстрее и точнее. Как только вы решите, что вам нужна фреза, перед вами встанет вопрос: покупать ли станок с ЧПУ или ручную фрезу. Выбор сводится к вашему бизнес-плану ».
Если вы хотите выполнять явно индивидуальную и ручную работу, то ЧПУ может оказаться излишним. «Но если вы хотите создавать стандартизированные конструкции и продавать их в больших количествах, станок с ЧПУ – что-то вроде Tormach 770M – в значительной степени не проблема.Они не только помогут вам работать быстрее, но и помогут добиться того, чего вы никак не можете сделать по-другому ».
Необходимые аксессуары для ЧПУ
Как и многие другие инструменты в вашем магазине, заготовка – это важный компонент головоломки. В конце концов, инструмент бесполезен, если вы не можете правильно использовать его в своей работе. «Я купил систему поддонов примерно через 8 секунд после того, как купил свой 770, и с тех пор я не снимал ее с машины более нескольких раз. Обработка заготовок – это как минимум полдела с ЧПУ », – объясняет Сорреллс.
Как и любой крупный магазин, если вы хотите быть прибыльным в качестве производителя ножей, вам необходимо действовать эффективно. Это означает поиск способов легко перемещать и разрезать сырье и готовые детали. «Вам нужно пополнять запасы и распределять запасные части с минимальными усилиями, насколько это возможно. А в небольшой производственной среде вам нужно быстро переключаться между заданиями. Поэтому для производителей ножей решающее значение имеет система поддонов. Причина этого (в отличие от использования тисков) в том, что большинство частей ножа плоские. Они просто не умеют ладить с тисками.”
Инструменты, которых вы могли не ожидать
«Я купил токарный станок до того, как купил фрезу. Это была ошибка. Оглядываясь назад, я бы сначала купил мельницу и плоскошлифовальный станок, – объясняет Сорреллс.
Но это не значит, что в цехе по изготовлению ножей нет необходимости в токарном станке. «На самом деле есть хороший аргумент в пользу чего-то вроде Tormach Slant-Pro почти для всех, кто делает папки [складные ножи]. Возможность изготовления нестандартных шарниров, стоек, пальцев, распорок и т. Д.дает вам возможность производить уникальные детали, чтобы отличать ваши ножи от ножей производителей, которым приходится полагаться на стандартные детали от поставщиков. А если вы производственный или полупроизводственный цех, преимущества автоматизации очевидны ».
Сорреллс считает, что если вы собираетесь заняться производством высокопроизводительных ножей, есть еще пара инструментов, которые могут вам помочь. Ленточная пила с автоматической подачей Tormach AF50 и фрезерный станок с ЧПУ 24R будут полезны, если вы хотите сделать много ножей.«Очевидно, что некоторые из этих вещей будут излишними, если вы только начинаете свой бизнес в качестве производителя ножей», – объясняет он.
Слова мудрости от ветерана по изготовлению ножей
Сорреллс занимается изготовлением ножей и мечей уже более десяти лет, но он всегда добавляет новые техники и инструменты в свой репертуар. Он не начинал с ЧПУ, но он изучил инструменты и теперь использует свою мельницу и шлифовальный станок Tormach для изготовления множества ножей. «YouTube – это крупнейший прорыв в обучении людей с тех пор, как в средние века был изобретен университет.Многие из ребят, у которых я больше всего узнал, – это ребята из Тормаха на Youtube ».
Когда его спросили, есть ли у него какие-нибудь советы для начинающих производителей ножей, он сказал: «Главное, что нужно понимать при изготовлении ножей (и это верно для любого другого предприятия на планете Земля), – это то, что если бы это было легко, всем» буду делать это. Когда вы покупаете инструмент, знайте, что вам нужно научиться. Не попадайтесь в ловушку, думая, что если бы у вас был лучший песчаный клин, вы были бы Тайгером Вудсом. Практически каждый инструмент, который вы покупаете, сначала борется с вами.Будьте терпеливы, держитесь, продолжайте работать с этим. Следующее, что вы знаете, это будет второй натурой. Вот тогда вы начнете производить более качественную продукцию, быстрее и с меньшим стрессом ».
Вы можете проверить канал Уолтера Соррелла на YouTube здесь: https://www. youtube.com/channel/UCkLxJCuQZ4hStBfs8TCnT9Q
Начало изготовления ножей – какое оборудование мне нужно?
Мы проводим довольно много курсов по изготовлению ножей в кузнице Тхарва Вэлли, поэтому неудивительно, что мы получаем много вопросов от студентов о том, как заняться изготовлением ножей в домашних условиях.
Как и в любом творческом поиске, мы встречаем множество людей, которые откладывают начало производства ножей, потому что у них нет выбора; С другой стороны, мы видим довольно много людей, которые бросаются покупать огромное количество дорогостоящего оборудования, но не имеют представления, как им пользоваться.
Когда дело доходит до создания ножей, самое важное – это не ваше оборудование, способности или знания. Это твое отношение. Если вы понимаете свой бюджет и подходите к покупке оборудования как к инвестициям, а не как к расходам, вы сможете заняться изготовлением ножей приятным и экологически безопасным способом.
Если вы встанете на правильную ногу, изготовление ножей может стать окупаемым занятием. Многие производители ножей начали с использования этого простого метода: вычислили свой первоначальный бюджет на инструменты и материалы и поместили эти деньги на отдельный банковский счет или в копилку / коробку для обуви / матрас. Это ваш фонд для изготовления ножей – когда вы покупаете оборудование и материалы, деньги поступают отсюда, когда вы продаете ножи, деньги возвращаются сюда. Сначала вы будете субсидировать производство ножей, а через некоторое время производство ножей, вероятно, окупится.
Вы можете заняться изготовлением ножей менее чем за 500 долларов с базовой настройкой удаления материала. Хотя вам, возможно, придется отправить лезвия для термообработки, вы быстро научитесь достаточно быстро перейти к промежуточной настройке, не тратя деньги на неправильный комплект.
Стартовый комплект (500 долларов США)
Если у вас нет инструментов, это то, что вам нужно для изготовления простых ножей путем снятия припуска.
- Верстак
- Угловая шлифовальная машина 5 “(резка и формовка заготовок)
- Диски угловой шлифовальной машины 1 мм (отлично подходят для вырезания фигур)
- Хороший набор напильников (фаски)
- Наждачная бумага с зернистостью 180, 320 и 600
- Малый сверлильный станок (без него сложно сделать прямые отверстия)
- Тиски для скамейки (купите или сделайте сами)
- Заготовки для лезвий Pre Cut (идеально подходят для ваших первых ножей)
- 3 мм 1075 Сталь (легко работать, легко поддается термообработке)
Rhynowet – наша предпочтительная наждачная бумага.Приблизительно по той же цене, что и покупка мокрой и сухой бумаги в строительном магазине, эта бумага служит почти в три раза дольше и работает лучше. Мы обнаружили, что это экономит час на одно лезвие по сравнению с другой наждачной бумагой.
Как только вы освоитесь со своим Starter Kit и начнете замечать, как он вас ограничивает, возможно, пора взглянуть на установку более среднего уровня. Это значительно дороже, но ваш более высокий уровень навыков поможет вам вернуть деньги, продавая более качественные ножи.В свою очередь, новое оборудование даст вашим навыкам возможность расти, чтобы вы могли заплатить за переход на следующий уровень, когда перерастете эту установку.
Промежуточный комплект (2000-4000 долларов)
Эта установка ускоряет процесс изготовления ножей, а также дает возможность изучить более сложные методы.
- Стартовый комплект, плюс:
- Ленточно-шлифовальный станок с регулируемой скоростью (1600 – 3200 долларов)
- Дисковый шлифовальный станок (1000 долларов США)
На этом этапе вам следует подумать о приобретении лучшего ленточно-шлифовального станка, который вы можете себе позволить.Хорошая шлифовальная машина может покрыть плохую поковку, но плохая шлифовальная машина даст вам плохую отделку, независимо от того, насколько хороша ваша поковка. Шлифовальные машины Noob – это универсальный вариант для большинства производителей ножей, который стоит вложений, если учесть, что каждый изготовленный вами нож в какой-то момент будет касаться измельчителя.
Когда вы только начинаете, ручное шлифование – хороший способ узнать, как ведет себя металл. Но после определенного момента ваше время лучше потратить на другие дела. Реверсивная шлифовальная машина с 9-дюймовым диском и регулируемой скоростью позволяет сэкономить часы на ручной чистовой обработке ножа и является лучшим способом получить плоскую поверхность.Рассматривая свои расходы, помните, что наждачной бумаги хватит только на одно или два лезвия, прежде чем ее можно будет использовать на ручках. Для достижения наилучших результатов используйте аэрозольный клей, чтобы прикрепить тонкий слой резины или картонной коробки для хлопьев к диску, затем используйте аэрозольный клей, чтобы прикрепить наждачную бумагу к резине или картону.
Если вы подумываете о покупке этого типа оборудования, вам следует подумать о добавлении регулятора скорости, чтобы максимально использовать типы материалов, с которыми вы можете работать. Хотя вы можете приобрести шлифовальные и шлифовальные машины со встроенными регуляторами скорости, более экономичным вариантом является использование регулятора скорости с частотно-регулируемым приводом (VFD).Если вы покупаете шлифовальный станок и шлифовальный станок с трехфазными двигателями, вы можете использовать контроллер скорости VFD совместно с обоими устройствами (что сэкономит вам около 600 долларов). Кроме того, контроллеры с регулируемой скоростью продлевают срок службы ремня, поэтому вы сэкономите много денег на ремнях. В течение срока службы кофемолки вы, вероятно, потратите на ремни в три раза больше, чем на покупку кофемолки.
Через некоторое время вы можете почувствовать желание перейти к чему-то новому. Многие производители ножей именно здесь решают заняться ковкой.
Ковочный комплект (2500–3000 долларов)
Ковка не только позволяет перемещать горячий металл, но и позволяет выполнять другие операции, такие как термообработка и сварка.
- Стартовый комплект, плюс
- (дополнительно) Промежуточный комплект, плюс
- Forge (600 долларов)
- Наковальня ($ 900 +)
- Flypress (300-800 долларов)
- Щипцы (200 долларов США за 5 пар)
- Молотки (200 долларов)
Ковка не обязательна для изготовления ножа, и она не даст лучшего лезвия (по крайней мере, для новичков и среднего уровня навыков).Независимо от того, хотите ли вы потратить много лет на овладение искусством ковки лезвий или просто стучать по горячей стали, ковка – это очень весело. Помимо изучения металлургии, вы получите неплохую тренировку: многие люди с удивлением обнаруживают, насколько физически требовательна ковка.
Ковкатакже является отличным способом сэкономить на инструментах, поскольку позволяет изготавливать собственные клещи, молотки и другие инструменты для изготовления ножей. Если это звучит привлекательно, возможно, стоит рассмотреть наш пятидневный курс по основам кузнечного дела, на котором вы будете развивать свои навыки, а также инструменты.В конце курса вы получите набор основных инструментов и газовую кузницу, а также навыки их использования.
После этого у вас, вероятно, будет достаточно знаний и опыта, чтобы определить свои следующие шаги. Описанные выше схемы обеспечивают прочную основу для развития и совершенствования по мере расширения ваших навыков изготовления ножей. Вы можете заинтересоваться изготовлением ножен, скримшингом или изготовлением дамасской стали. Вы можете даже решить заняться изготовлением ножей в качестве коммерческого предприятия, например, в качестве мастера по изготовлению лезвий, изготовителя производственных ножей или учителя.Оборудование становится более дорогим вложением, но потенциальная прибыль соизмерима.
- Стальная ленточная пила (1200 долларов)
- Ленточная пила по дереву (600 $)
- Печь для термообработки (2500 долларов США)
- Гидравлический кузнечно-прессовый пресс 25 т (7000 долл.
США)
- Power Hammer, 25 кг (10 000 долл. США)
- Сталепрокатный стан (2 000 долл. США)
- Твердомер по Роквеллу (2000 долларов США)
- Устройство для сшивания кожи Tippmann Boss (2600 долларов)
Ваши интересы будут направлять вас к ресурсам и сообществам, которые будут способствовать вашим будущим инвестициям в изготовление ножей, а изготовленные вами лезвия помогут финансировать ваши занятия по мере того, как вы продолжаете учиться и расти.Начав с правильного отношения, вы настроите себя на то, чтобы заниматься изготовлением ножей так, чтобы это окупалось.
Информационный центр изготовителя ножей своими руками: набор инструментов для начинающих
Хотите начать производство ножей? Хотите собрать основные инструменты? Возможно, у вас уже есть многие из необходимых вам инструментов.Инструменты
Хотя список инструментов изготовителя ножей будет сильно различаться в зависимости от того, кого вы спросите, я составил список основных инструментов, которые помогут вам начать работу. К счастью, многие из них распространены в гаражах по всей стране.
Рабочий стол – Стол или другое прочное рабочее место. Должен быть примерно подходящего роста для работы стоя.
Тиски – обязательно. Что-то, что сдерживает вашу работу. Вы можете обойтись без зажимов и тисков, но хорошие тиски прослужат вечно и будут одной из самых полезных вещей в вашем магазине.
Hacksaw – Для начала подойдет любая приличная ножовка с качественным лезвием. Выбирайте биметаллические лезвия хорошего качества. Биметалл означает, что зубья сделаны из другого металла (и твердости), чем окружающее лезвие.Lennox, Starrett, Milwaukee, DeWalt – хорошие бренды.
Напильники – По крайней мере, два больших фрезерных напильника, полуторный и один гладкий. Я предпочитаю довольно крупный, скажем, 12 дюймов. Марка Nicholson признана хорошей. Ручки не являются обязательными, но облегчают работу с напильниками.
Drill – Вам нужно будет просверлить сталь и материал для ручек. Обычная аккумуляторная дрель – это хорошо для начала, но в конечном итоге сверлильный станок дает наилучшие результаты.
Биты – Обязательно наличие хорошо укомплектованного перечня острых сверл, подходящих для сверления стали.Сверла из быстрорежущей стали идеально подходят для сверления всех видов отожженной стали. Кобальт лучше, но и дороже.
Молоток – Вам понадобится как минимум один молоток. 20 унций. мяч pein – удобный выбор, чтобы носить его с собой в магазине.
Центровочный перфоратор – Брызги для центрального перфоратора. Это поможет держать эти биты на цели и сделает нож более профессиональным.
Деревянная рашпиль – для придания формы ручке из дерева или синтетики.
Зажимы – Зажимы и тиски разных размеров для зажима во время склеивания.
Линейка – Возьмите линейку из нержавеющей стали с дюймами и сантиметрами. В ближайшие годы вы найдете множество применений для этого.
Перманентные маркеры – Это могут быть ваши лучшие друзья. Тонкий или сверхтонкий наконечник. Черный или любой другой цвет, который есть в продаже.
Наждачная бумага в ассортименте – Для придания формы, сглаживания и полировки вам понадобится наждачная бумага для мокрого / сухого типа с зернистостью от 60 до 600.
Деревянные блоки – Сделайте себе несколько деревянных блоков для удержания наждачной бумаги.Очень полезны обрезки дуба или клена, которые красиво и квадратно нарезаны, а также дюбели разного диаметра.
ИМХО, это все, что вам действительно нужно для начала работы. Попробуй. Многие удивительные ножи изготавливаются с помощью напильников и наждачной бумаги.
Если вам действительно нравится ваше новое хобби:
ОБНОВЛЕНИЯ:
Настольный ленточный шлифовальный станок – комбинированная дисковая / ленточная шлифовальная машина размером 1 дюйм x 30 дюймов или 4 дюйма x 36 дюймов.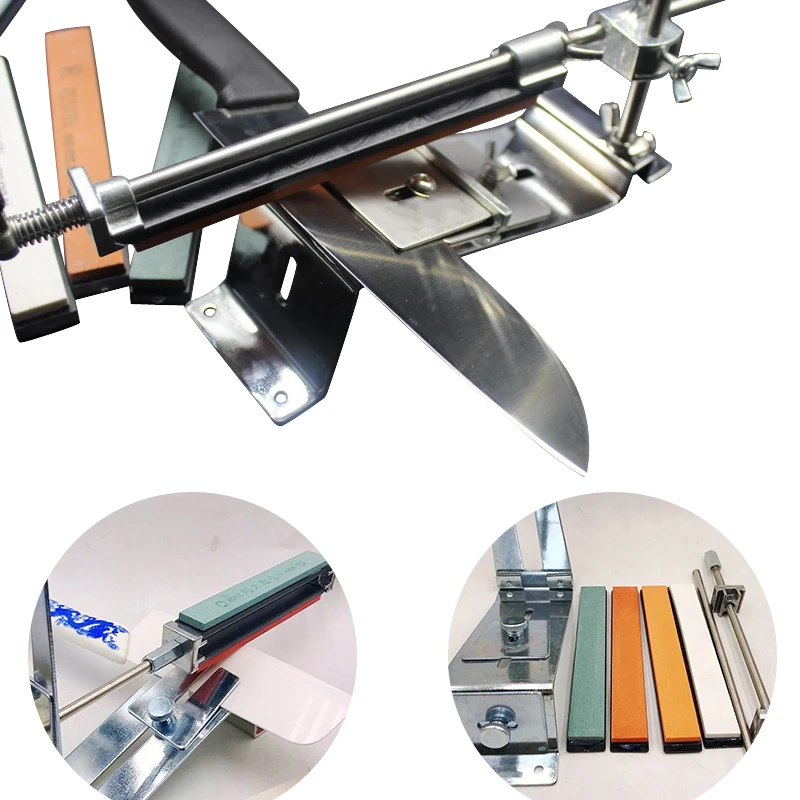
Drill Press – Не должно быть изысканным. Стол должен быть под прямым углом к биту.
Ленточная пила – Ленточная пила по металлу. Переносные ленточные пилы можно переоборудовать для работы на верстаке.
Для основной термической обработки …
Описываемая здесь шестерня предназначена для термической обработки самой простой углеродистой стали, такой как 1080 или 1084. Эти стали рекомендуются для начинающих, поскольку их можно успешно подвергать термообработке с минимальным оборудованием.
Есть несколько способов закаливания.Достаточно простой и чистый способ – использовать пропан или газ MAPP.
Огненный кирпич – Небольшую кузницу для начала можно сделать из двух огнеупорных кирпичей с мягкой изоляцией. Вы также можете сделать «кузницу для супа» для термической обработки простой углеродистой стали, но кузница из двух кирпичей проверена и очень проста в изготовлении. Погуглите “два кирпичных кузницы” или посмотрите на YouTube, и все готово.
Горелка с вихревым наконечником – Горелка с вихревым наконечником Bernz-O-Matic, такая как TS-8000, подходит для двухкирпичных кузниц.Его кружащееся пламя перемещает тепло. Избегайте использования этих паяльных горелок с карандашным наконечником, поскольку они фокусируют тепло в крошечном пятне. Мы хотим большого тепла. Найдите слова «Swirl» и «MAPP-совместимый».
Сжиженный нефтяной газ или газ MAPP – Мое правило – баллон и запасной баллон. Вы не можете выбежать во время термообработки. Бутылки с пропаном в стиле кемпинга (не канистры) подойдут. Желтые баллоны с газом MAPP хороши, если вы коваете что-то большое, толстое или длиннее, чем предназначена для вашей кузницы.MAPP горит сильнее, чем пропан.
Растительное масло – Вам понадобится как минимум два галлона растительного масла. Дешевое масло – это нормально.
Резервуар закалки – Растительное масло нужно перелить в какой-нибудь металлический контейнер.
Перчатки – Защитите руки кожаными перчатками. Избегайте рабочих перчаток, у которых есть нейлон на суставах пальцев, так как они могут расплавиться и вызвать неприятный ожог. (личный опыт разговоров) Сварочные перчатки хороши.
Магнит – Подойдет любой старый магнит.Я использую старый магнит динамика от автомобильной стереосистемы.
Щипцы – Вам понадобится чем-нибудь, чтобы схватить раскаленное лезвие. У некоторых есть настоящие кузнечные щипцы. В крайнем случае подойдет старый комплект тисков.
Духовка – Любая духовка, способная нагреваться до 200 ° C (400 ° F) и вмещающая нож, который вы собираетесь изготовить. Тостер отлично подходит для этого, так как вы можете вынести его в гараж и избавиться от этих странных запахов на кухне.
Термометр для духовки – Если вы не доверяете циферблату на тостере, (а кто?) Термометр для духовки даст вам лучшее представление о том, насколько нагревается тостер.
Огнетушитель – Посмотрим … пламя, горячая сталь и масло … хммм … вам лучше иметь.
СИЗ …
Респиратор – Как минимум несколько приличных пылезащитных масок N95. Лучше заглянуть в респиратор-полумаску.
Защитные очки – Надеюсь, самоочевидно.
Перчатки – См. Раздел термической обработки.
И не забывайте свет! Хорошо освещенное рабочее место всегда будет вам на пользу.
Удачи!
Пожалуйста, дайте мне знать, если я что-то пропустил,
Дан
Я собрал бесплатный PDF-файл с этим основным списком.Скачивайте и распространяйте бесплатно.
Как сделать нож
Как сделать нож
Искусство и наука изготовления ножей – одно из старейших ремесел человека. Любой, у кого есть несколько торговых инструментов, навыки их использования, желание и время, может создать свой собственный нож. Ножи можно сделать «с нуля», используя металлическую заготовку для лезвия и дерево или другие материалы для рукояти. Ножи также можно сделать из покупных наборов. Лезвия ножей «Сделано с нуля» изготавливаются одним из двух методов: зачисткой или опиливанием и шлифовкой; или ковка, также называемая «кузнечное дело».«Удаление материала проще всего сделать в магазине товаров для хобби, и это можно сделать с помощью нескольких ручных и электрических инструментов. Ковка требует гораздо больше опыта и инструментов.
Мы показываем изготовление ножа с фиксированным лезвием и рукояткой со сплошным хвостовиком. Дизайн, а также детали пошаговой конструкции принадлежат моему сыну Майклу Берчу, который занимается изготовлением нестандартных ножей на полную ставку (www.burchtreeblades.com). Хотя у Майкла есть целый магазин машин, созданных специально для изготовления ножей, он показывает, как использовать простые ручные инструменты и несколько «трюков» для создания собственного ножа.«Изготовление ножей может быть очень опасным, – говорит Майкл. «Всегда надевайте защитные очки, а не только очки, а при сильном шлифовании – респиратор и средства защиты органов слуха».
Нож можно собрать, используя только лезвие, заготовки рукоятки и булавки, а также несколько ручных инструментов. Однако электроинструменты значительно упрощают и ускоряют работу.
Изготовление ножей своими руками: подходящие материалы
Майкл использует кусок прутка 1095 размером 1-1 / 2 на 7-1 / 2 дюйма.«Доступны многие виды стали, но сталь 1095 дешевая, с ней легко работать и при правильной термообработке; делает отличное лезвие. Покупайте горячекатаный или отожженный, если таковой имеется, так как с ним легче работать. Не используйте мягкую сталь, которую можно купить в местных магазинах, так как эта сталь предназначена для сварки ».
Для рукоятки ножа используются заготовки из орехового дерева. Лучшая древесина для рукояток ножей – это древесина твердых пород и даже лучше; профессионально стабилизированная древесина. Стабилизатор заполняет поры древесины химическим веществом, защищающим древесину от порчи.Стабилизированная древесина не только служит дольше, но и ее легче шлифовать и обрабатывать. Стабилизированную древесину можно приобрести у поставщиков, производящих ножи, или вы можете «стабилизировать» свою собственную древесину с помощью Minwax Wood Hardener. Создайте стабилизирующий инструмент из каменной кладки и дренажного штуцера для тормозной магистрали, который можно купить в магазинах автозапчастей.
Дерево, используемое для ручек, должно быть стабилизировано с помощью отвердителя Minwax Wood Hardener. Самодельный стабилизатор можно сделать из банки Мэйсона и дренажного штуцера тормозной магистрали.
«Установите воздухоотводчик через отверстие в крышке банки и сделайте герметичное уплотнение», – говорит Майкл.«Поместите древесину в банку, добавьте отвердитель для древесины и качайте ручку, пока из древесины не начнут выходить пузырьки. Это означает, что поры древесины заполняются отвердителем. Делайте это очень медленно и осторожно. Не переусердствуйте с вакуумом и всегда надевайте защитные очки. Ослабьте вакуум, затем удалите заготовки, заверните в полиэтиленовую пленку и дайте дереву медленно высохнуть ».
В показанном ноже также используется стержень из нержавеющей стали 3/16 дюйма для штифтов и трубка из нержавеющей стали 1/4 дюйма для отверстия под ремешок.Оба доступны в магазинах бытовой техники с полным спектром услуг, таких как Ace Hardware.
Пока древесина застывает, Майкл начинает работать с заготовкой лезвия. «Создайте на бумаге полноразмерный узор лезвия и обведите его фломастером на заготовке. Используя металлический кернер, нарисуйте начальные ямки для ряда отверстий по внешнему краю контура. Ямочки должны быть расположены немного дальше, чем полный диаметр сверла, и на половину диаметра от контура.Затем, используя сверло Cobalt в сверлильном станке, просверлите отверстия. Работайте медленно, смазывайте сверло смазочно-охлаждающей жидкостью и не позволяйте металлу становиться слишком горячим, иначе вы можете «закалить» сталь. Опять же, наденьте защитные очки и убедитесь, что бланк надежно зажат, чтобы не произошло «вертолетного движения», когда бита застревает в металле. Отметьте места отверстий для штифтов и ремешка, а также просверлите их ». Майкл использует насадку для снятия фаски, чтобы немного снять фаску с отверстий.
(слева) Первый шаг – создать узор для лезвия.Обратите внимание, что у показанного ножа лезвие с полным хвостовиком. (Справа) Используйте пробойник, чтобы отметить места последовательных отверстий, которые необходимо просверлить, по контуру лезвия.
(слева) С помощью хорошего кобальтового сверла в сверлильном станке просверлите отверстия по контуру лезвия. (Справа) Показана просверленная заготовка, готовая к вырезанию и приданию формы.
После того, как все отверстия будут просверлены, зажмите заготовку полотна в тисках на прочном верстаке и просто «соедините точки», прорезав между отверстиями хорошей биметаллической ножовкой.Естественно, ленточная пила для резки металла делает эту работу быстрее и проще.
(слева) Используйте ножовку, чтобы «соединить точки», или прорежьте металл между отверстиями. (Справа) Показана необработанная заготовка.
«Теперь самое интересное – придать форму клинку», – говорит Майкл. Традиционный метод – это подача, но это требует времени и усилий. Зажмите заготовку лезвия в хороших твердых тисках и, используя новый плоский напильник, подпилите заготовку до контура.Используйте файловую карту, чтобы очистить файл от металлических опилок. Всегда держите файл под углом 90 градусов к заготовке. Вертикально-шлифовальный станок, такой как шлифовальный станок 1 на 42, быстро заточит профиль ». Поставьте под кофемолку ведро с водой, чтобы уловить искры и надеть все предохранительные приспособления.
(Слева) Старомодным способом придания формы лезвию ножа является использование хорошей поперечной фрезерной пилки для подпиливания и протяжки металла. (Справа) Нож / ленточно-шлифовальный станок с регулируемой скоростью облегчает работу.
Затем найдите центр острия ножа. С помощью толстого маркера отметьте нижний край заготовки. Поместите заготовку на гладкую плоскую поверхность и используйте остроконечное сверло, диаметр которого немного меньше толщины стали, чтобы разметать осевую линию. Просто скатайте сверло по краю, переверните заготовку и снова сверните, создав две линии на лезвии шириной около 1/16 дюйма.
Прикрутите заготовку лезвия к твердому верстаку так, чтобы лезвие выступало за край.Используйте пилку для цепной пилы, чтобы создать линию «врезания» (где заканчивается скос) на задней части лезвия. Затем воспользуйтесь напильником для придания формы лезвию, следуя как контуру стороны лезвия, так и отмеченной центральной линии на нижнем крае. Опять же, это требует времени и усилий, но если бланк надежно прикреплен, вы удивитесь, насколько быстро выполняется рутинная работа. Повторите с противоположной стороны. Закройте создаваемый скос толстым острием Sharpie и подпилите его, чтобы найти высокие и низкие точки на лезвии.
(Слева) Заготовка грубой формы готова к сверлению. (Справа) Найдите и просверлите отверстия для штифтов ручки и, если необходимо, отверстие для шнурка, используя сверлильный станок. Также неплохо просверлить дополнительные отверстия в области рукоятки, чтобы облегчить нож и обеспечить лучшую балансировку.
Чтобы найти центр кромки лезвия ножа, используйте толстый «Sharpie», чтобы зачернить кромку, затем поцарапайте или начертите центральную линию, положив заготовку на гладкую плоскую поверхность и прокатав сверло той же толщины, что и лезвие, по краю.
(слева) Теперь самое интересное. С помощью фломастера создайте узор по форме лезвия. Закрепите заготовку шурупами на прочном верстаке. Затем используйте пилку для цепной пилы, чтобы отметить «линию погружения» или место остановки лезвия. Сделайте это с обеих сторон лезвия. (Справа) Используя хороший напильник для фрезерования, нарисуйте лезвие для придания формы. Используйте файловую карту для частой очистки файла.
«Теперь вы готовы установить заготовки для ручек», – говорит Майкл.Слегка отшлифуйте заготовку лезвия, а также ручки, чтобы убедиться, что все они гладкие и плоские. Поместите малярную ленту на внешнюю сторону одной заготовки ручки и прижмите ее к заготовке лезвия. Просверлите отверстия в лезвии и в заготовке. Снимите заготовку и отметьте внутреннюю часть, затем повторите для другой заготовки ручки. Нарисуйте контур заготовки лезвия на заготовках ручки и обрежьте их по форме с помощью ленточной пилы, оставив ручки немного завышенными.
Обрежьте штифты и трубку с ремешком, чтобы немного увеличить длину.«Вставьте булавки в портативную электрическую дрель и используйте наждачную бумагу, чтобы слегка придать им шероховатость и немного утончать, чтобы они вошли в отверстия. Они должны плотно входить в отверстия рукоятки и лезвия, но не слишком плотно. Если слишком туго, они могут расколоть материал ручки », – объясняет Майкл. Установите заготовки рукоятки на лезвие и вставьте штифты и трубки на место. Отшлифуйте рукоятку и заготовку лезвия до нужной формы. Снимите ручки, отметьте передний профиль и грубо отшлифуйте их до нужной формы ».
Затем лезвие следует подвергнуть термообработке.Хотя профессиональные производители ножей используют кузницу и печь, традиционные примитивные методы также подойдут.
Лезвие должно быть подвергнуто термообработке, и хотя Майкл использует точное специальное оборудование, чтобы максимально использовать потенциал своих лезвий, он предложил «примитивную термическую обработку», которая позволит создать отличный нож без использования печи или кузницы. «Вам понадобится закрывающийся контейнер с арахисовым маслом и хороший раскаленный костер. Хорошо работает огонь из живой изгороди, потому что он горит очень горячо. Дайте огню сгореть до раскаленных углей и вставьте лезвие в угли с помощью пары длинных металлических щипцов ». 1095 должен достигнуть 1475 градусов, чтобы стать «критическим» – термин, используемый для объяснения того, когда состав стали начинает переходить в «аустенитный».
Хотя не совсем такая же температура; многие производители используют магнит, чтобы узнать, когда сталь начинает аустенизироваться. Для проверки лезвия подойдет магнитный «пикап» из автомобильного магазина. Как только лезвие станет немагнитным, оставьте его на несколько минут, чтобы оно достигло истинной «критической» температуры, а затем дайте ему остыть до черного цвета.Сделайте это несколько раз, чтобы «нормализовать» лезвие. В третий раз нагрейте лезвие до температуры и быстро охладите лезвие в арахисовом масле. После остывает; очистите лезвие и проведите напильником по краю. Край должен быть «гладким», и напильник будет скользить по нему, а не врезаться.
«Теперь о темперировании, – говорит Майкл, – после закалки в арахисовом масле лезвие твердое, но чрезвычайно хрупкое. Отпуск снижает твердость и ломкость стали.Установите кухонную духовку на 400 градусов и готовьте на лезвии в течение 2 часов. Оберните лезвие парой слоев алюминиевой фольги, чтобы избежать неприятного запаха во время приготовления. Дайте остыть и повторите; теперь ваше лезвие подверглось термообработке! ”
Заготовка лезвия подвергается окончательной обработке на ленточно-шлифовальном станке.
Следующий шаг – закончить лезвие. «Лезвие должно быть надежно зажато. Используйте наждачную бумагу 3-M Imperial Wet / Dry, которую можно приобрести в любом магазине O’Reilly’s или в других автомагазинах.«Начните с максимально возможной зернистости, чтобы избавиться от царапин – Майкл обычно начинает с зернистости 320, но это после их шлифовки до гладкой поверхности. Закрепите наждачную бумагу бруском квадратной микарты или куском сплющенного дерева. Смажьте наждачную бумагу струей Rem-Oil, WD-40 или Windex. Это помогает убрать песчинки во время шлифования. Затем обработайте зерно под углом 45 градусов, чтобы удалить царапины от предыдущего зерна. Шлифуйте, пока не добьетесь желаемой отделки, Майкл обычно заканчивает с зернистостью от 800 до 1000, но обработка с зернистостью 400 (называемая обработкой вручную) по-прежнему выглядит великолепно.Очистите 45-е, зачистив горизонтальные линии от углубления до кончика.
(Слева) Прикрепите одну заготовку ручки к заготовке лезвия и отметьте контур ручки и расположение отверстий для штифта и ремешка. Повторите то же самое для противоположной заготовки ручки. (Справа) Заготовки ручки готовы к грубой распиловке для придания формы на ленточной пиле по дереву, сабельной или копировальной пиле.
(Слева) Слегка отшлифуйте штифты и трубку ремешка и снимите фаски с отверстий в заготовке лезвия.(Справа) Постучите по булавкам и трубке ремешка, чтобы временно удерживать ручки на месте.
(Слева) Приблизительно сформируйте ручку с помощью деревянного рашпиля или ленточной шлифовальной машины и отметьте валики, затем снимите ручки и обрежьте их, чтобы очертить и придать им форму. (Справа) Убедитесь, что тыльная сторона рукоятки и заготовка лезвия очень плоские и гладкие.
«Очистите лезвие медицинским спиртом, чтобы удалить все масла, и немного смочите его в хлористом железе, чтобы« протравить »лезвие и удалить« хамон ».«Уксус сделает то же самое, но займет немного больше времени. Затем протрите его пищевой содой, чтобы нейтрализовать травитель, и несколько раз нанесите последний слой абразива. Если вы хотите «пометить» свой клинок, местный магазин трофеев может добавить ваше имя.
(Слева) Используйте эпоксидную смолу, чтобы приклеить заготовки ручки к заготовке лезвия и постучать по штифтам и трубке ремешка на месте. Дайте настояться на ночь. (Справа) Продолжайте формировать ручки деревянными рашпилями. Обернув лезвие и закрепив лентой для защиты, используйте тонкую полоску шлифовальной ленты, чтобы придать форму и отполировать область ручки.
«Теперь пора приклеить ручки. Сожмите их вместе, чтобы края ручки были ровными с обеих сторон, и обработайте их до желаемой зернистости ». Майкл предлагает нанести немного WD-40 на лезвие и обернуть его бумажным полотенцем, прикрытым липкой лентой, чтобы защитить лезвие при надевании рукояток. Разложите вощеную бумагу, медицинский спирт, ватные палочки, зажимы и 2-тонную 30-минутную эпоксидную смолу Devcon. (Пятиминутная эпоксидная смола сохнет слишком быстро.) Зачистите хвостовик и немного обработайте, чтобы эпоксидная смола имела более липкую поверхность.Очистите все участки медицинским спиртом и смешайте большое количество эпоксидной смолы. Оберните штифты эпоксидной смолой и простучите ими через одну сторону ручки, затем приклейте ручки и постучите по штифтам насквозь. Зажмите ручки вниз, используя ватные палочки, чтобы удалить излишки эпоксидной смолы. Дайте высохнуть на ночь (принесите в дом, если в магазине / гараже слишком холодно).
Ленточно-шлифовальный или шлифовальный станок с постепенно уменьшающейся зернистостью бумаги упрощает и ускоряет чистовую обработку ножа.
«Когда все высохнет, отшлифуйте булавки», – говорит Майкл.«Не торопитесь – вы можете очень легко нагреть булавки и обжечь дерево вокруг них». Для придания рукоятке формы используйте хороший деревянный рашпиль или шлифовальную машину. В этом случае поможет заслонка Scotchbrite, вставленная в дрель. Обработайте наждачной бумагой. Отшлифуйте, пока ручки не станут гладкими и без царапин, затем нанесите масло тунга или датское масло.
«Очевидно; уровень отделки полностью зависит от вас. Процесс занимает много времени; но награды потрясающие ».
(слева) Используйте лоскут Scotchbrite для создания гладкой полированной поверхности.(Справа) Для дальнейшего сглаживания ручки можно использовать более мелкие кусочки наждачной бумаги с все более мелким зерном.
(слева) Крошечные кусочки наждачной бумаги, обернутые вокруг буровой штанги, сглаживают трубку с отверстием для ремешка. (Справа) Датское масло втирается рукой в область рукоятки.
(Слева) Затем лезвие затачивают, сначала используя алмазную шлифовальную головку. (Справа) На следующем этапе используйте керамическую хонинговальную головку.
… Готовый нож
Подробнее…
Майкл Берч из Burchtree Bladeworks создал множество уникальных стилей ножей, которые очень популярны среди коллекционеров. Посетите www.burchtreeblades.com .
Рекомендуемые статьи
Хобби изготовления ножей
Искусство изготовления ножей – очень полезное хобби для тех, кто разбирается в руках.И одна из замечательных особенностей этого хобби заключается в том, что в итоге у вас получается что-то очень функциональное, когда вы это делаете.
И, как и в любом другом хобби, существует множество способов изготовления ножей. Для некоторых способов понадобится кузница и наковальня. Здесь изготовление ножей перекликается с хобби или ремеслом кузнечного дела. (Здесь у меня есть введение в кузнечное дело). Но сделать ножи можно без кузницы и наковальни. И таким образом можно делать совершенно профессиональные ножи.В этом вводном руководстве я объясню вам этот метод изготовления ножей и покажу вам необходимые инструменты и материалы. У меня также есть два видео прямо на этой странице, которые вы можете посмотреть. Они показывают полный процесс изготовления ножей. Они находятся внизу этой страницы.
На этом рисунке показан нож, который я сделал методом снятия припуска. На картинке также показаны несколько деревянных кусков, которые можно использовать для рукояток ножей. Слева направо древесина ручки – кокоболо, красное дерево и кап.
Два основных метода изготовления ножей
Метод ковки ножа. Когда мы думаем о изготовлении ножа, мы чаще всего думаем об этом.Как кузнец лепит нож с кузницей и наковальней. Это, конечно, отличный способ сделать его, но это может занять много времени и довольно дорого. В этом методе кузнец берет кусок стали и выковывает ему форму ножа. Ему доводят почти готовую форму, а затем обрабатывают с помощью нескольких инструментов, таких как шлифовальный станок и точилки.
Метод удаления запасов. Этот метод является гораздо более простым и требует меньших финансовых затрат. Хотя на это еще нужно время.Что происходит, так это то, что изготовитель ножей получает кусок стали нужной толщины и размера больше, чем желаемый нож. Затем он использует режущие и шлифовальные инструменты, чтобы получить законченную форму ножа. Вы просто удаляете весь лишний инвентарь, пока не останется только нож. После этого сталь закаляется и отпускается, затем полируется и затачивается.
Ручки, захваты и др.
Есть еще один аспект изготовления ножей, который мне особенно нравится.Это аспект дизайна и изготовления ручки. В этом аспекте хобби у вас есть большой выбор, и вы можете получить массу удовольствия. Этот аспект практически не зависит от того, как вы сделали лезвие ножа. Так что независимо от того, кузнеете вы его или снимете, вы можете сделать любую ручку, какую захотите.
A Краткий обзор процесса
(Этот процесс предназначен для метода удаления материала) Нож, изображенный в верхней части этой страницы, был изготовлен с использованием этого процесса.
- Вы рисуете точный узор ножа, который хотите сделать – в масштабе
- Перенесите этот узор на кусок стали
- Вырежьте сталь с помощью различных инструментов, включая шлифовальный станок, ножовку, ювелирную пилу, пока профиль или очертание ножа не станет правильным.
- Вы используете напильники для снятия фаски лезвия и выполнения любых деталей и тонкой работы.
- Закалка лезвия с помощью источника тепла
- Закалите лезвие с помощью источника тепла, чтобы смягчить некоторые его части
- Сделайте ручку из дерева или другого материала
- Прикрепите ручку и обработайте ее шлифованием
- Отполировать лезвие и рукоять
Обзор необходимых инструментов и материалов
Материалы – Самое важное – это сталь, которую вы собираетесь использовать для изготовления настоящего ножа.Если вы используете метод удаления материала, у вас есть ограниченные возможности. Если бы вы ковали нож, вы могли бы взять практически все, что было стальным, и преобразовать его в нож. Для этого подойдут такие вещи, как железнодорожный шип или автомобильная рессора. Даже старый файл.
Но я рекомендую вам приобрести официальный кусок стали, который идеально подходит для изготовления ножей. Существует много разных типов стали, и все они имеют разные характеристики, обычно в зависимости от того, сколько в ней углерода.Но для наших целей я рекомендую вам взять кусок стали 01. У него отличные характеристики ножа, и с ним довольно легко работать.
Вот идеальный кусок на amazon.com. Это инструментальная сталь толщиной 1/8 дюйма и длиной 18 дюймов, поэтому вы можете получить из нее один очень длинный нож или два девятидюймовых ножа: Инструментальная сталь O1 (закалка в масле) Плоский приклад, шлифованный, ASTM-A681-94, толщина 1/8 дюйма, ширина 2 дюйма, длина 18 дюймов (это именно тот кусок стали, который я купил для изготовления ножа для этого урока)
Эта сталь доступна во многих местах.Вы можете искать инструментальную сталь 01. Просто помните, что он должен быть достаточно большим для вашего ножа и важна его толщина. Его толщина составляет 1/8 дюйма, что делает его хорошим прочным ножом.
Дерево для ручки
Для изготовления ручки вам понадобится кусок дерева или другой материал. Вы можете купить что-то, называемое весами для ножей, которые представляют собой кусок дерева, выбранный для изготовления ножей. Часто они уже приходят разрезанными на две части для каждой половины ручки.Для этого урока я использовал вот это: Деревянный нож Amboyna Burl Scale
.Инструменты
У вас есть некоторая гибкость, и вы можете много импровизировать в зависимости от того, какие инструменты у вас есть. Но для начала вам понадобится ножовка, чтобы вырезать основную форму ножа.
Ножовка по металлу, напильник, настольный шлифовальный станок, рашпиль по дереву
Тогда вам понадобится какой-то способ придать ему правильную форму. Ножовка порежет только прямые линии, поэтому вам понадобится какой-то другой инструмент, чтобы получить эти кривые.Настольная шлифовальная машина идеально подходит для этого. Но если у вас нет настольного точильного станка, вы можете использовать хороший фрезерный напильник. Однако это займет некоторое время. Поэтому, если вы используете ножовку и пилку, я рекомендую вам делать как можно больше ножовки, чтобы упростить подпиливание. Вам также понадобится деревянный рашпиль, чтобы придать форму вашей ручки. .
Источник тепла
Необработанный кусок стали нельзя использовать в качестве ножа, пока вы его не закалите и не закаляете. Закалка означает повышение температуры лезвия примерно до 1500 градусов по Фаренгейту.А закалка доводит его до 450-600 единиц. Вы можете добиться этого тепла с помощью небольшой кузницы на заднем дворе, как у меня, или вы можете просто использовать горелку bernzomatic, как у сантехников. Вы можете купить их в любом строительном магазине.
Бумага Emory
Это действительно то, что вам нужно, но не обязательно. Для очистки и полировки лезвия вы используете самые разные зерна от 100 до 600. В этом уроке я использовал 100-600 с интервалами зернистости 100 для полировки лезвия.
Прочее прочее
Для выполнения такой работы требуется несколько различных инструментов, которые вы можете найти или импровизировать, включая зажимы для удержания предметов, щипцы или плоскогубцы для манипулирования лезвием при нагревании и тунговое масло для полировки рукоятки. Также вам понадобится заклепка и клей, чтобы прикрепить ручку к лезвию. Я использовал деревянные дюбели 1/4 дюйма. Также можно использовать латунные заклепки.
Как сделать нож
Это краткий обзор с фотографиями процесса.
Вы вытягиваете свой нож на бумаге в точном размере и масштабе. Затем приклейте его к куску стали, как показано на рисунке. Видите, насколько большая сталь подходит для всего ножа? И обратите внимание, как я разместил его по как можно большему количеству краев. Это сводит к минимуму количество резки, которое мне нужно делать.
Теперь используйте все инструменты, которые у вас есть, чтобы вырезать нож. Это называется профилированием лезвия.
Я сделал большую резку ножовкой.Но ножовка режет только прямые линии, поэтому я обработал профиль настольным шлифовальным станком.
После этого я перешел к использованию фрезерного файла, чтобы получить профиль именно там, где он должен быть.
Вот что у вас получается. Профиль вашего ножа. Вы также можете видеть, что я просверлил два отверстия, чтобы можно было прикрепить ручку.
Затем вы используете фрезерный напильник для заточки скоса лезвия.Это та часть лезвия, которая будет затачиваться. И это по обе стороны от лезвия.
Теперь о нагреве и отпуске. Вы используете какой-то источник тепла, чтобы довести температуру примерно до 1500 F. Здесь он будет светиться красным оранжевым светом. Как вы узнаете, что он находится при нужной температуре, с помощью магнитного теста. Вы часто проверяете это магнитом. Он будет держаться, пока не достигнет нужной температуры.Как только он перестанет прилипать, быстро окуните весь нож в ведро с маслом. Это блокирует затвердевание.
Закалка – Как только масло охладится до комнатной температуры в масле, вы счистите всю образовавшуюся черную окалину и снова нагреете ее. На этот раз только частично. Вы хотите нагреть его так, чтобы тыльная сторона лезвия стала синей, а режущая кромка стала пшеничного цвета. Это делает его более мягким по спинке и твердым по режущей кромке, чтобы он сохранял остроту и остроту.Если вы используете фонарик, вы можете рисовать с помощью фонарика, чтобы получить правильные цвета. Если вы используете огонь, как у меня на картинке, поместите нож рядом с огнем задним краем, как показано на рисунке.
Как только вы установили нужную цветовую температуру, вы снова погасите ее в огне. Он закален и закален.
На этом этапе вы можете пойти дальше, зажать лезвие и пройтись по бумаге emory, начиная со 100, чтобы получить желаемую отделку лезвия. Не нужно забывать о запахе.Он будет накрыт ручкой.
Теперь сделаем и прикрепим ручку. Вы используете острие ножа в качестве шаблона для грубого стрижки рукоятки. При необходимости разрежьте его пополам, чтобы у вас остались две половинки. Но сделайте эту предварительную ручку больше, чем нужно. И плотно прикрепите его к ножу. Вы будете отключать его, поэтому не усложняйте его.
Теперь зажмите нож и с помощью деревянного рашпиля доведите рукоять до окончательной формы.Конечно, вам часто придется перемещать зажимы и находить разные удерживающие позиции. Придайте ему почти окончательную форму.
Удалите штифты, нанесите эпоксидный клей на обе половинки ручки и приклейте их, повторно проклеив. После того, как он высохнет, вы можете отшлифовать его, чтобы получить окончательную форму ручки.
Я использовал 5-минутный двухкомпонентный эпоксидный клей гориллы.
Теперь вы можете нанести несколько слоев тунгового масла или кипяченого льняного масла, чтобы отполировать ручку.Слегка отшлифуйте между слоями и высыханиями.
Хорошо, заточите нож на точильный камень и готово!
Видео изготовления ножей
Это серия из двух видеороликов, которые демонстрируют полный процесс изготовления ножей от начала до конца.
В части 1 этого урока я покажу вам, как выбирать сталь и как выполнять резку, шлифование и профилирование.Готовим нож для закалки и отпуска.
В этой части руководства по изготовлению ножей мы завершаем нож закалкой, отпуском, изготовлением / прикреплением рукоятки, затем полировкой и шлифовкой.
Ресурсы, книги и многое другое
Это серия из двух видеороликов, которые демонстрируют полный процесс изготовления ножей от начала до конца.
КНИГИ ДЛЯ НОЖА
Изготовление ножей на заказ: 10 проектов от мастера
Расширяя пробел между предварительно нарезанными и «художественными» ножами, с пошаговыми иллюстрированными инструкциями по созданию уникальных и красивых ножей. Узнайте, как создавать собственные проекты или конструкции: кухонный нож для очистки овощей; Универсальный нож Full-Tang; Нож для разделки с частичным хвостовиком; Шкуросъемник через хвостовик; Нож дикой природы; Кованый походный нож; Кухонный измельчитель; Карманный нож однолезвийный; Складной нож Lockback; Кинжал из дамасской стали.
Магазин ножей Уэйна Годдарда за 50 долларов, исправленный
– Раскрывает секреты изготовления прочных ножей, не тратя много денег – Обращается к готовой аудитории: BLADE Show – крупнейшая выставка нестандартных столовых приборов в США ежегодно привлекает 10 000 человек – Представляет простые, экспертные инструкции в полноцветных фотографиях
Мастера ножей, ветераны и новички, знают и доверяют методам и обучению Уэйна Годдарда, и это показывает уровень мастерства, представленный на национальных выставках ножей.Сама книга, которая изменила лицо кузнечного дела, обновлена: теперь в нее добавлены полноцветные фотоинструкции и проверенные временем производители ножей, к которым будут обращаться долгие годы.
-Инструменты, необходимые для изготовления ножей и оснащения личной мастерской без лишних затрат.
-Методы ковки и термообработки для улучшения существующих навыков изготовления лезвий
– 200+ цветных фотографий демонстрируют основные приемы изготовления ножей.
Самым простым руководством по изготовлению ножей является “Магазин ножей” Уэйна Годдарда за 50 долларов, пересмотренный.
Полное онлайн-руководство по изготовлению ножей, ИНСТРУМЕНТЫ ТОРГОВЛИ – Изготовление ножей Berg
Перечислен ассортимент инструментов для ножевых мастеров. Многие из этих инструментов или оборудования относительно дороги. Каждый человек должен определить, сколько денег он хочет вложить в это металлическое ремесло. Некоторым может хватить ножовки, чтобы вырезать каждый профиль лезвия, или использовать напильник для создания скосов лезвий.Другие вложат немного денег и купят угловую шлифовальную машину, которая сделает большую часть профильных работ. Те, кому нравится это ремесло, со временем вложат деньги в три или четыре ключевых оборудования для изготовления ножей. В порядке важности это ленточно-шлифовальный станок 2×72, сверлильный станок, кузница и ленточная пила. Сможете ли вы выполнить работу без этих инструментов? Да, но наличие подходящего инструмента для работы делает ее намного более приятной и оставляет мастеру больше времени, чтобы посвятить художественным аспектам ремесла.Обратите внимание, что в дополнение к перечисленным инструментам и оборудованию кузнецу ножей также потребуется множество более обычных инструментов, таких как плоскогубцы, молоток, тиски и различные зажимы.
Угловая шлифовальная машина
Один из наименее дорогих способов вырезать ножи из стали – это использование угловой шлифовальной машины и отрезного круга. Угловые шлифовальные машины также могут использоваться с плоскими шлифовальными кругами для профилирования надрессорных балок и даже для масштабирования грубых форм. При шлифовании металла эти инструменты выделяют много искр, поэтому необходима надлежащая защита глаз.
Наковальня
Для лезвий ручной ковки очень важна хорошая наковальня. Наковальни следует закрепить на прочной платформе на удобной высоте. Если вы собираетесь делать только лезвия для удаления припуска, наковальня может не потребоваться.
Ленточная пила
Ленточная пила для резки металла может использоваться для точного вырезания формы каждого ножа. Если вы собираетесь инвестировать в ленточную пилу, убедитесь, что это пила для резки металла, а не ленточная пила, предназначенная для дерева.Два недорогих варианта – это переделать Portaband от Harbor Freight, который можно установить на столе, или купить вертикальную / горизонтальную ленточную пилу и использовать ее в вертикальном или вертикальном положении. Любой вариант подойдет, но в любом случае рекомендуется сразу покупать лезвие хорошего качества. Лезвия, которые поставляются с пилами Harbour Freight, можно сразу выбросить. Еще один вариант – поиск подержанного оборудования для механических цехов. Коммерческие ленточные пилы могут стоить тысячи, но иногда бывшие в употреблении могут быть вполне доступными.
Ленточно-шлифовальный станок
Пожалуй, самый важный инструмент для ножевода. Шлифовальная или шлифовальная машина 2×72 дюйма является стандартом в отрасли. Шлифовальные машины используются для обработки дерева, а шлифовальные машины – для шлифования стали. Несмотря на то, что эти универсальные станки могут делать и то, и другое, большинство производителей ножей называют их ленточно-шлифовальными станками, потому что в большинстве случаев они используются для придания формы лезвиям и шлифования скосов. Многие совершают ошибку, покупая недорогую 4-дюймовую ленточную шлифовальную машину Home Depot, а затем обнаруживают, что без модификаций очень сложно шлифовать хорошие фаски.Проблема в том, что у большинства 4-дюймовых ленточных шлифовальных машин нет плоской плиты с открытыми сторонами, которая необходима для того, чтобы лезвие можно было врезать с обеих сторон для создания скосов с линиями врезания. Другие начинающие кузнецы по лезвиям покупают ленточные шлифовальные машины диаметром 1 дюйм, которые имеют плоскую плиту и необходимое пространство с каждой стороны, но большинство из них просто недостаточно мощны. Они могут выполнить свою работу, но шлифовка фаски может занять буквально часы, а не минуты. Стандартные шлифовальные машины 2×72 производятся постоянно растущим ассортиментом компаний.Они могут иметь множество вариантов. Регулируемая скорость, упоры для инструментов и возможность превращения в горизонтальную шлифовальную машину – это лишь некоторые из них. Эти машины сильно различаются по стоимости и срокам доставки. Для тех, кто серьезно относится к изготовлению ножей, рекомендуется шлифовальная машина мощностью 2 л.с. с регулятором скорости. Новичок может потратить 150 долларов на ленточную шлифовальную машину Home Depot или несколько сотен на 1-дюймовую шлифовальную машину, а вскоре после этого пожелать сэкономить на приличной машине. Некоторые производители предлагают доступные варианты, чтобы получить 2х72 новичка.Вы можете приобрести базовое шасси, включая плоскую опору, ведущие колеса и опорные колеса. Затем вы можете пойти и купить мотор отдельно и пропустить регулировку скорости, если вы не можете себе это позволить. Наконец, вы можете построить для него свою собственную подставку из дерева или стали. Собрав все вместе таким образом, новичок может приобрести качественную шлифовальную машину 2×72 примерно за 800 долларов. Это все, что вам нужно для начала и получения красивых лезвий. По мере прохождения можно добавлять такие опции, как большие контактные круги для полых шлифовальных скосов, небольшие насадки для шлифования небольших участков, наклонные столы для легкого шлифования скосов и насадки для плоского шлифования.
В комплекте с ленточно-шлифовальным станком вам понадобится ассортимент ремней. Большая часть материала будет удалена с помощью крупнозернистой ленты. Для грубого шлифования основной массы материала мы используем зерно 36 или 60. Для отделочных работ будет использована более мелкая крупа. Ленты с крупным зерном нагреваются меньше, чем ленты с мелким зерном
Типы ремней
Керамические ремнипредназначены для влажного или сухого использования и очень прочны. Лучше всего они работают при шлифовании под давлением, что на самом деле помогает сохранить остроту волокон ленты.Керамические ленты долговечны и быстрее всего удаляются. К сожалению, керамические ленты с мелким зерном не доступны.
Оксид алюминия отлично подходят для абразивных материалов общего назначения. Его можно использовать влажным или сухим. Оксид алюминия обычно является лучшим выбором для лент с более мелким зерном.
Цирконийможно использовать как влажным, так и сухим, и для сохранения остроты зерна требуется сильное давление. Он отлично подходит для шлифования нержавеющей стали. Цирконий дороже, но дольше, чем ленты из оксида алюминия.
Scotch Brite – это разновидность полировальных лент, которые продаются под разными названиями.Они отлично подходят для отделочных работ и полировки скосов.
Войлочные ленты можно использовать с полировальной пастой или без нее.
Доступны кожаные или кожаные ремни для полировки фаски.
Пробковые ремни имеют толстую пробковую основу и оксид алюминия, защищающий от истирания.
Полировальный круг
Настольный шлифовальный станок с полировальными кругами может стать огромным преимуществом в любом магазине ножей. Эти полировальные круги в сочетании с правильным составом используются для полировки латунных валиков, булавок, многих акриловых красок и аллюмилитных чешуек.Старайтесь использовать каждое полировальное колесо только для одного материала. Например, не полируйте латунь тем же кругом, который вы используете для полировки пластмасс. Смешивание различных компонентов снижает эффективность каждого из них. Кроме того, небольшие кусочки латуни на колесе могут создать царапины на любом мягком полированном пластике.
Разметчик по центру
Этот маленький гаджет, скорее, скорее инструмент, чем часть оборудования, очень важен, если вы хотите получить хорошие скосы.Доступны несколько различных дизайнов. Вы хотите выбрать тот, который позволяет вам установить высоту писца. В итоге вы захотите провести две параллельные линии на краю лезвия, которые называются железнодорожными путями. Эти линии служат визуальным ориентиром при шлифовании скосов. Не покупайте самоцентрирующиеся писцы, потому что они производят только одну центральную линию. валики и даже профилирующие весы. Многие используют дисковые шлифовальные машины со сменными пластинами, каждая из которых имеет шлифовальные круги с более мелким зерном для плоской полировки.
Dremel Grinder
Эти портативные мини-шлифовальные машины, которые часто упускаются из виду, отлично подходят для придания формы ручкам и очистки небольшого внутреннего радиуса профиля заготовки ножа, когда небольшая насадка для шлифовального круга 2×72 недоступна. Их также можно использовать для создания Choil Notches и Jimping.
Сверлильный станок
Как и ленточная пила, вы получаете то, за что платите, со сверлильным станком. Небольшие сверлильные станки доступны в местных магазинах бытовой техники и могут показаться доступными по цене. Просто будьте осторожны и убедитесь, что сверлильный станок можно замедлить настолько, чтобы просверлить металл.Поначалу многие тратят часы на сверление отверстий под штифты электродрелью. Они выгорают сверла или в конечном итоге приводят к упрочнению материала лезвия. Способность сверлильного станка прилагать адекватную направленную вниз силу при медленных оборотах позволяет легко просверливать отверстия в стали.
Дисковая шлифовальная машина
Дисковые шлифовальные машины доступны в различных размерах. Они могут быть настольными, отдельно стоящими, вертикальными или горизонтальными.Дисковые шлифовальные машины с пластиной с плоской поверхностью в сочетании с регулируемой подставкой для инструмента отлично подходят для получения идеально плоского помола
Тиски для ножа
Особый предмет, специально разработанный для удержания ножа за лезвие, не поцарапав его. Тиски для ножей обычно предназначены для вращения для простоты использования. Подходит для ручного шлифования.
Фрезерный станок
Хотя это не является обязательной частью оборудования для ножевого цеха, наличие небольшого фрезерного станка позволяет легко фрезеровать небольшие зазубрины Choil и Jimping.
Резервуар для закалки в масле
Этот резервуар используется для хранения закалочного масла, используемого во время термообработки. Резервуар должен быть из стали. Будьте достаточно устойчивы, чтобы не опрокинуться, и имейте крышку, которую можно использовать, чтобы при необходимости погасить пламя. Нефтяные резервуары могут быть вертикальными или горизонтальными и часто изготавливаются из стальных труб или труб.
Дисковая пила для игл
Эта миниатюрная разделочная пила, конечно же, не является обязательным оборудованием для ножевого цеха.У Harbour Freight есть один примерно за 30 долларов. Мы купили его, чтобы посмотреть, как он работает, и теперь он нам очень нравится. Он позволяет быстро и легко резать латунные штифты, а также режет штифты, не оставляя заусенцев. Намного проще, чем ножовка, ленточная пила или угловая шлифовальная машина.
Плунжерное приспособление
Плунжерное приспособление изготовлено из двух металлических частей, в которых просверлены и нарезаны отверстия, позволяющие соединять их вместе на лезвии, как зажим. Они действуют как защита от случайного заточки за плоский край приспособления.Они помогают мастерам лезвий создавать ровные линии врезания фаски с обеих сторон лезвия. Их часто можно использовать в сочетании с скользящим приспособлением, если приспособление предназначено для врезного приспособления, или их можно использовать при шлифовании фаски от руки.
Закалочное ведро и подставка
У ножеводов должно быть ведро с водой, расположенное рядом с ленточно-шлифовальным станком. Мы рекомендуем сделать подставку из дерева или металла, чтобы вам не приходилось постоянно нагибаться, чтобы закалить горячие лезвия. Это делает измельчение немного более комфортным.
Спиральная пила
Свиток или булавочная пила очень удобны при обрезке материала шкалы до нужного размера. Мы используем спиральную пилу, чтобы отрезать доступный материал с чешуи после того, как каждая сторона была прикреплена к лезвию.
Шаблоны для снятия фаски
Доступно множество различных типов зажимов для снятия фаски. Наиболее распространенными, кажется, являются скользящие приспособления. Они прикрепляют лезвие к зажимному приспособлению и имеют возможность регулировки угла скоса. Эти выдвижные приспособления протягиваются вдоль рабочего стола шлифовального станка под углом 90 градусов.Они просты в использовании, относительно недороги и позволяют создавать одинаковые фаски с обеих сторон лезвия. Некоторые даже предназначены для работы с приспособлением для погружения. Обратной стороной использования этих приспособлений является то, что иногда бывает трудно добиться того, чтобы фаска соответствовала кривизне лезвия.
Наклонный стол
Наклонный стол – это рабочая подставка или приспособление для снятия фаски, которое авторы разработали, изготовили и продают. Он устанавливается на стандартный инструментальный рычаг 1 1⁄2 дюйма. Он был разработан для наших шлифовальных машин OBM 2×72, но может быть адаптирован к широкому спектру шлифовальных машин различных производителей.Это достигается за счет того, что он может быть прикреплен болтами к инструментальной консоли любого размера и регулируется по вертикали, горизонтали и даже может быть квадратным до плоского края плиты станка. Наклонный стол обеспечивает гибкость при шлифовании скосов. Это один из немногих приспособлений, который можно использовать для создания плоских скосов и полого шлифования. В основном стол устанавливается под желаемым углом скоса. Лезвие прижимается к столу и медленно поднимается до контакта с ремнем. Затем кузнец перемещает лезвие горизонтально, шлифуя ровную линию по заданным центральным линиям.Прелесть этой системы в том, что она дает изготовителю ножа полный контроль над лезвием. Он или она может наблюдать за начерченными линиями и при необходимости шлифовать больше в одной области. Если изготовитель ножей аккуратно шлифует до постоянной глубины вдоль разметанных осевых железнодорожных путей, то скос будет повторять кривизну лезвия. При использовании наклонного стола можно использовать небольшой цифровой угловой измеритель для записи угла стола. Эти счетчики доступны в Интернете по цене около 20 долларов. Они позволяют вам установить таблицу для одного угла скоса, записать этот угол, а затем иметь возможность переустановить таблицу на тот же угол в будущем.Это идеально подходит для шлифования грубых скосов для материала одной толщины, а затем для работы с ножом с другим углом наклона или перехода с плоской плиты на большой круг, а затем точно переустановить стол для окончательного окончательного шлифования после термообработки.
Наклонный стол можно также использовать вместе с от руки или при обучении шлифованию от руки. Мастера лезвий могут создавать точные грубые фаски с помощью наклонного стола и ленты для грубого шлифования. Это позволяет им создавать одинаковый угол скоса с обеих сторон лезвия.Это также экономит массу времени. С лентой для грубого зерна наклонный стол может создавать грубые фаски за считанные минуты. После термообработки они затем переходят в ручное шлифование с помощью ленты с более мелким зерном. Положите фаску прямо на плиту шлифовального станка или контактное колесо. Предварительно установленная фаска затем действует как направляющая для чистовых проходов. Для некоторых это лучшее из обоих миров.
Используйте стрелки влево / вправо для навигации по слайд-шоу или проведите пальцем влево / вправо при использовании мобильного устройства
.